Stay Informed With News and Insights from Tompkins Solutions
Discover the latest industry news and gain valuable insights into warehouse automation and supply chain management in today's complex global economy.
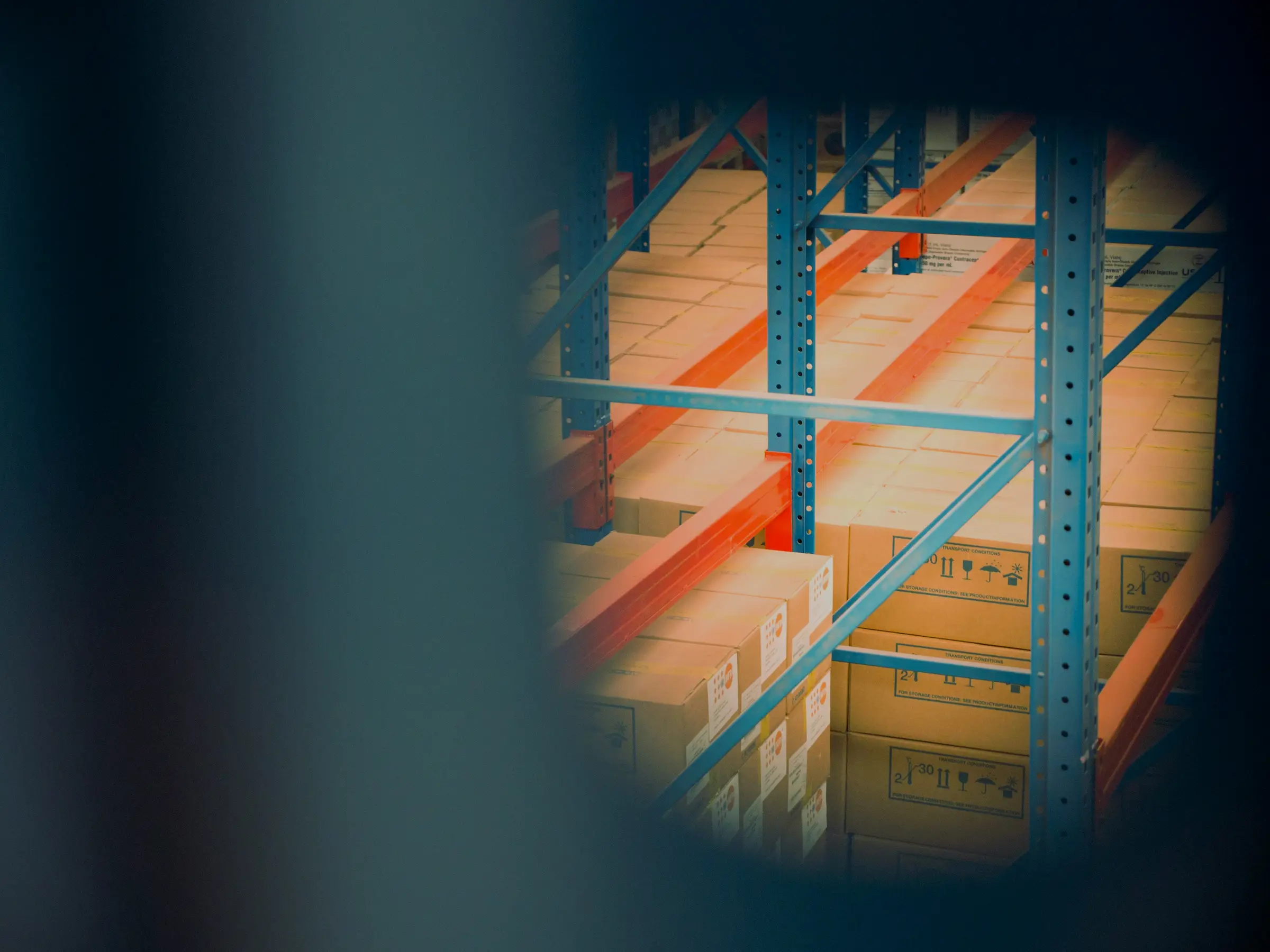
NEWS AND INSIGHTS
Featured Posts
Discover valuable resources to enhance your knowledge.
NEWS AND INSIGHTS
Latest Posts
Get the latest news and insights from our experts.
Thank you! Your submission has been received!
Oops! Something went wrong while submitting the form.