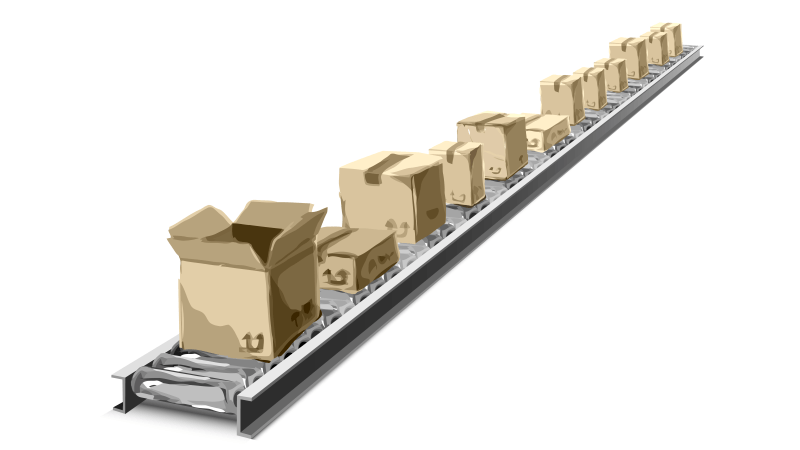
Karl Borgman
Project Manager, Tompkins International
Choosing the right conveyor system is critical to the success of the rest your automated material handling system. Conveyor systems are typically used to transport materials for long distances while reducing operational costs and improving safety. Systems include various types of transport and accumulation conveyors along with: merges, inclines, declines, spirals, scanners, diverts, and sorters. Floor conveyors can be utilized for various types of products, from small and light to full pallets, while overhead conveyors are configured for specific types of units depending on the application.
The typical conveyor system is a fixed path that optimizes the labor required to move product, provide accumulation as a buffer, and protect the product from damage due to excessive handling and improved operator safety for bulky or heavy product in warehouse and manufacturing applications. Flexible conveyors can be used independently or in conjunction with fixed conveyor systems
Typical conveyor uses can be for truck unloading and loading, transporting up or down between levels, pick engines, movement between manufacturing and staging, and to sorters and automated storage and retrieval systems.
Selecting which conveyor system best fits your needs requires evaluating several factors. Some things to consider are:
- Are full cases or single units going to be conveyed?
- Which conveyor system will be able to handle the product throughput? I.e. How many units per hour are flowing through it?
- What kind of dedicated space is available for the conveyor systems?
- Are the products in format that can be handled by the selected conveyor system? i.e. cases, poly bags, units, manufacturing units, etc.
There are many types of conveyors to choose from (Selection based on product and throughput rates), including:
- Gravity
- Roller
- Skate Wheel
- Ball Transfer
- Chute
- Powered
- Line-shaft Roller
- Belt Driven Live Roller
- Belt on Roller
- Slider Bed Belt
- Modernized Driven Roller
- Line Shaft Live Roller
- Wheel Presser
- Overhead conveyor
- Mergers
- Dual Line
- Saw Tooth
- Multi Line
- Diverts
- Deflector / Plow
- Pop Up Skewed Devices
- Diverter / Pusher
- Powered Pivot Diverter
- Pop-Up Chain Transfer
- Tilt Tray
- Slat Shoe
While conveyors can increase efficiency in many warehouses and manufacturing facilities, each application needs to be carefully evaluated and designed to work with the rest of the automated material handling system. In addition to carefully evaluating the engineering requirements of the conveyor system, the overall business requirements for each situation need to be considered, including capital expense, future maintenance costs, and future growth requirements.
How can we help improve your supply chain operations?
Schedule a consultation or contact Tompkins Solutions for more information.
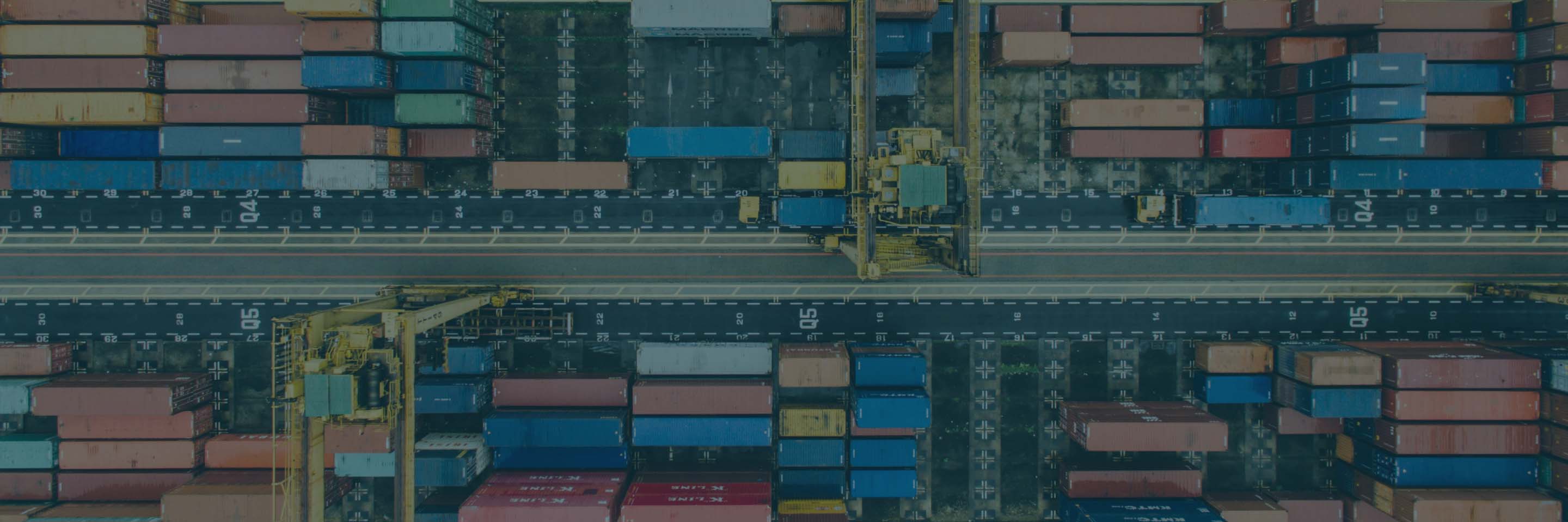
Featured Posts
Discover valuable resources to enhance your knowledge.