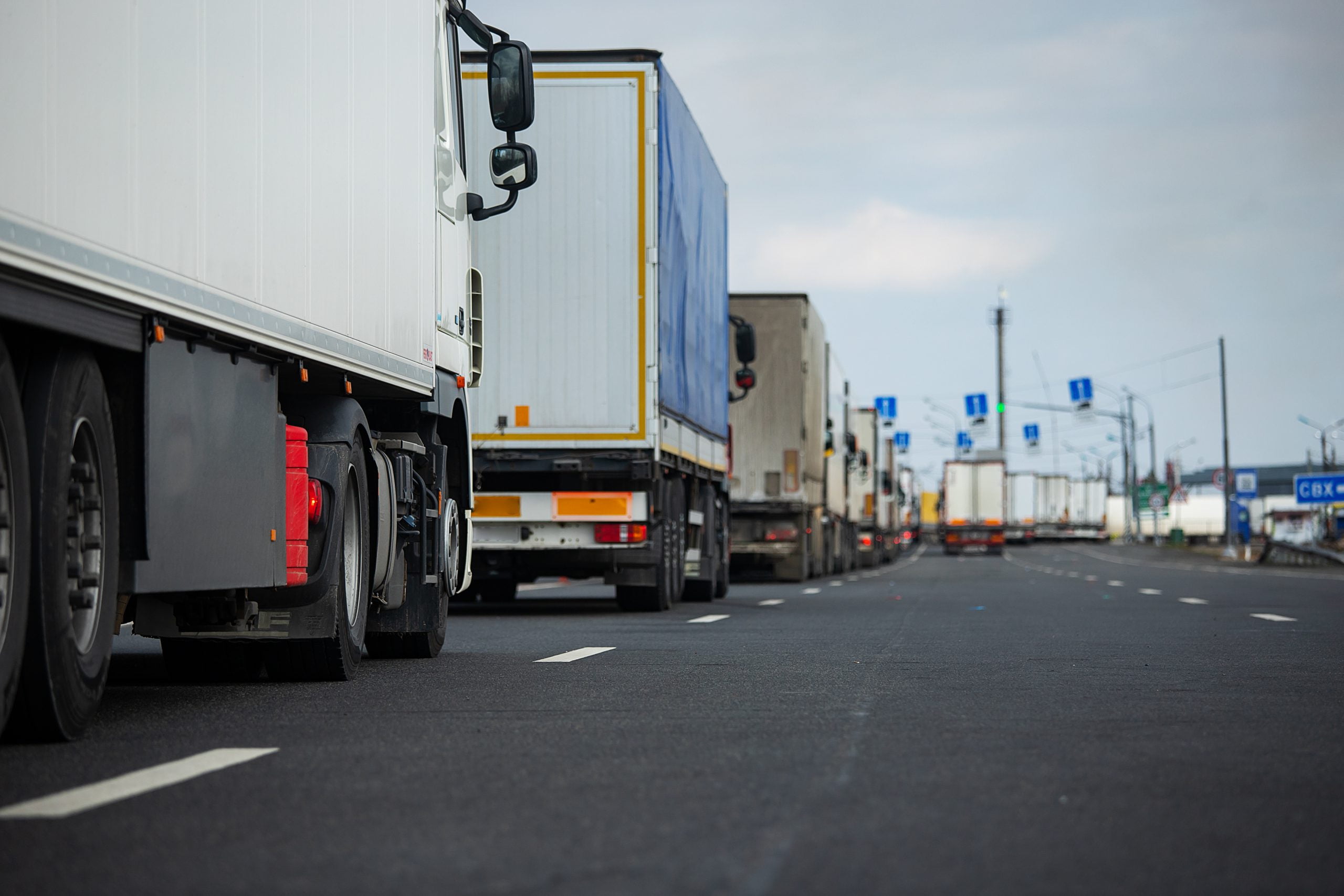
With today’s changing economy, trade tensions with China and an ongoing series of shortages, delays and disruptions, many companies are reevaluating their network design and looking to move supply chain operations closer to home. As increasing demand and lease rates are making it harder to acquire warehouse space in the United States, countries such as Mexico and Canada are emerging as popular options for companies to expand their logistics network across a wide variety of industries.
For companies that plan to maintain manufacturing facilities overseas, expanding your logistics network in Mexico or Canada can still offer many advantages. Below are five factors to evaluate to help determine if cross-border logistics is right for your company.
Product Values and Types: How much does a customer typically spend per order? Under the Section 321 statute, companies can ship orders valued at $800 or less from Mexico or Canada to the U.S. duty-free, resulting in millions of dollars in cost savings. In addition to order values, it’s also important to consider the types of products you’re shipping. For example, food and beverage items may lose quality when exposed to varying temperatures and are also one of the top targets for cargo theft, which can create additional challenges when shipping across borders.
Service-Level Agreements (SLAs): While both Mexico and Canada share long land borders with the U.S., going through customs can add an extra day to transit times, so companies that have strict 2-day delivery guarantees may not be able to meet customer expectations. Additionally, crossing the border out of Mexico typically takes longer than it does from Canada due to less entry points, more congestion and a higher number of drivers and/or trailers involved in each shipment.
Transportation Options and Costs: In addition to transit times, it is important to determine what modes of transportation are available and the costs for each. While both Mexico and Canada typically move items over the border by trailer, the launch of Falcon Premium and the recent merger between Canadian Pacific and Kansas City Southern will expand rail service throughout North America, providing more options for companies to ship freight across the three countries.
Real Estate and Labor Rates and Availability: Acquiring and affording warehouse space and labor continue to create challenges for logistics operations in the U.S., with experts predicting ongoing shortages and rising costs to remain through 2024. While these trends are also occurring across North America, lower labor rates and increased investments in industrial developments could create opportunities for companies looking to expand fulfillment operations into Mexico.
Software Solutions: Shipping across borders adds another level of complexity to logistics and fulfillment operations and requires the use of a robust technology stack. Software that provides end-to-end visibility and real-time tracking and updates on shipments can help ensure security and compliance and reduce time spent crossing the border. By integrating solutions such as a transportation management system (TMS) and inventory management system (IMS), companies can access accurate, up-to-date data to proactively identify any potential issues and make well-informed decisions to minimize costs and disruptions and ensure customer satisfaction.
Selecting the right location for your logistics network and operations requires careful planning and thorough analysis. With nearly 50 years of experience in supply chain network optimization, Tompkins Solutions can work with your company to create and implement the optimal network design to meet your current and future needs. Contact us today to learn how to optimize your supply chain network to increase resilience, minimize costs and continue to deliver on customer demands.
How can we help improve your supply chain operations?
Schedule a consultation or contact Tompkins Solutions for more information.
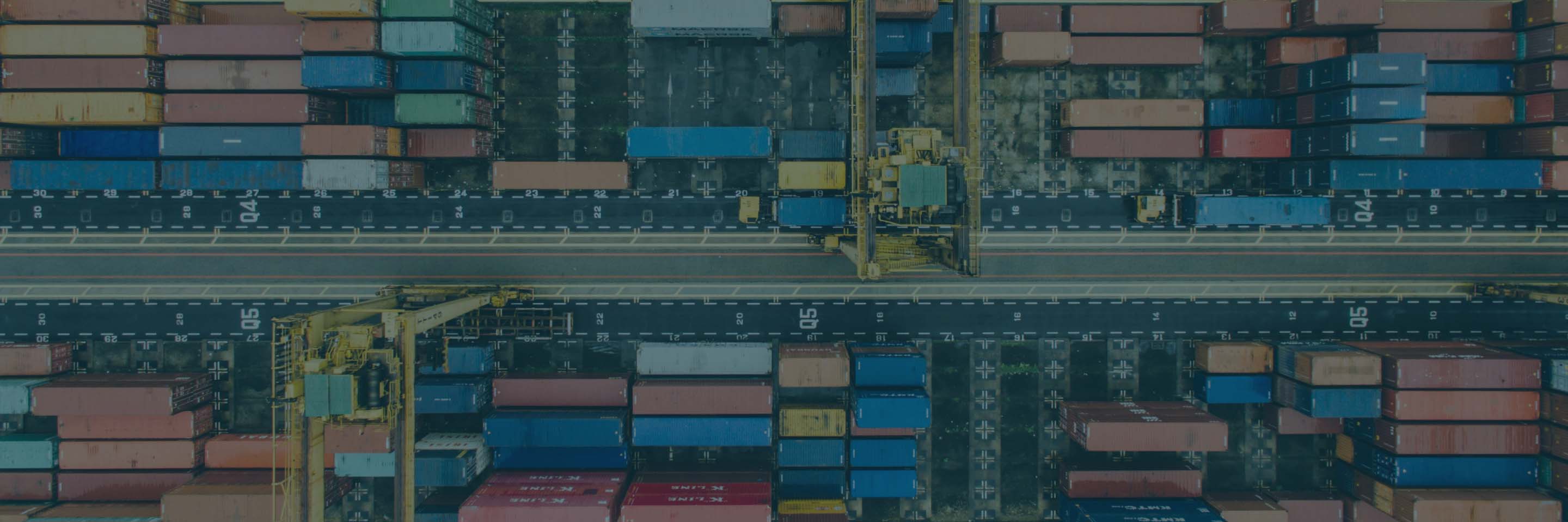
Featured Posts
Discover valuable resources to enhance your knowledge.