This article has been updated with the latest strategies for effective inventory management, including tips on inventory optimization, reverse logistics, and demand forecasting. Links to five related resources have been added to provide a deeper understanding of how businesses can enhance visibility, reduce costs, and meet customer demands.
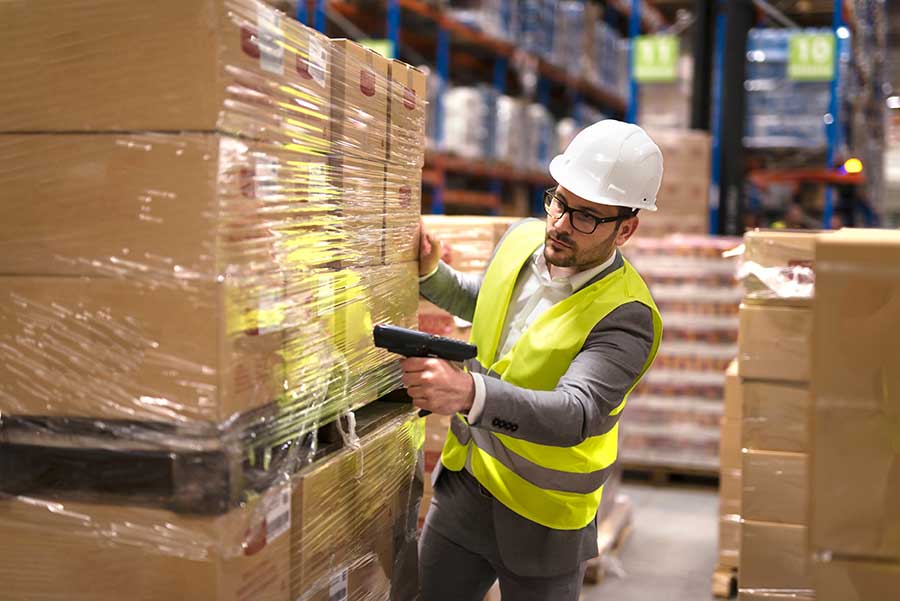
An effective inventory management strategy can significantly reduce redundant inventories throughout the supply chain, driving cost savings and improving overall efficiency. By aligning inventory with actual demand and optimizing store replenishment, businesses can ensure customer needs are met without overstocking or excess carrying costs.
Discover how to balance inventory levels in Inventory Management: How to Avoid Overstock and Stockouts While Maximizing Profits.
In today’s competitive landscape, inventory management has evolved from being a single-node operation to a collaborative process involving multiple stakeholders in the supply chain. Strategies such as inventory optimization and returns management help reduce stock levels while increasing service levels and ensuring availability for high-demand items.
Learn how improved forecasting techniques can enhance inventory efficiency in Inventory Management: How to Improve Demand Forecasting.
Reverse logistics is another essential component of modern inventory management. Businesses must streamline automated returns processing for ecommerce to recover value from returned products while ensuring they are reintroduced into inventory efficiently.
Explore how reverse logistics can benefit your inventory processes in How to Optimize Your Reverse Logistics Operations.
By incorporating retail inventory visibility systems and leveraging advanced tools like track-and-trace automation for pharmaceuticals, businesses can improve inventory control and meet customer expectations in industries like food and beverage. This ensures that products are available when and where they are needed, minimizing the risks of stockouts and overstocks.
For a comprehensive overview of key terms and strategies, visit Key Inventory Management Terms.
Effective inventory management also requires focusing on profitability. Leveraging advanced forecasting tools and streamlining supply chain processes can lead to better decision-making and improved margins.
Read more about strategies to enhance profitability in Increasing Profitability Through Inventory Optimization.
By embracing innovative tools and strategies, businesses can reduce inefficiencies, improve visibility, and ensure customer satisfaction in today’s fast-paced supply chain environment.
How can we help improve your supply chain operations?
Schedule a consultation or contact Tompkins Solutions for more information.
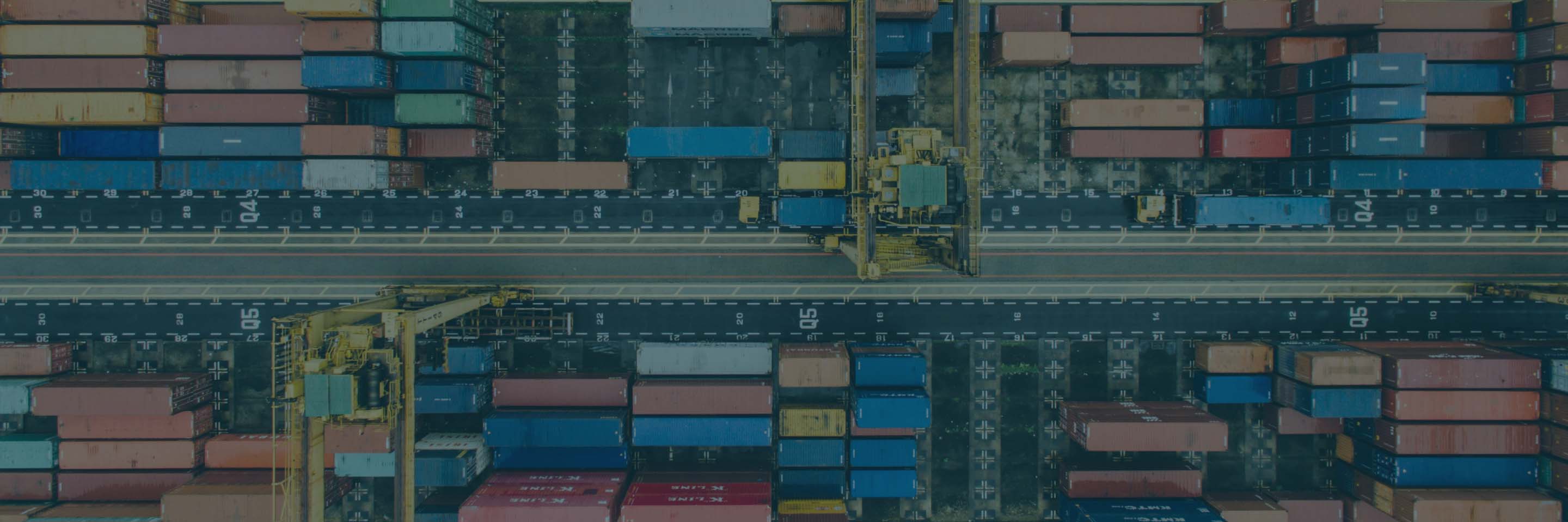
Featured Posts
Discover valuable resources to enhance your knowledge.