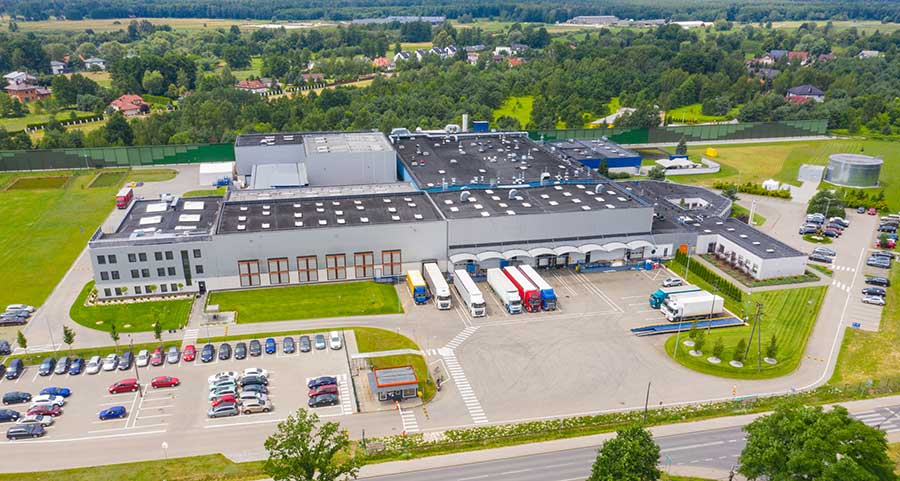
With the level of disruption and uncertainty in today's world, many brands and retailers are experiencing widespread change across their business and distribution operations. Continued e-commerce growth is prompting many companies to add new distribution centers (DCs) and fulfillment methods to cope with changing order profiles and volumes. Facility location planning is key to meeting those demands.
Steps for Successful Site Selection
The first step in any facility location planning is to complete the design of the new operation-not the actual building. In order to properly size the facility, you must first understand how it will function over the next several years. Selecting the right site or building can be a lengthy and costly process, so careful planning is required to avoid any potential mistakes at this stage.
When moving to another facility-whether existing or new-ensure the plot of land is large enough to accommodate your current and future operations, inbound and outbound truck access and ample parking for employee vehicles. If moving to a new area, now is also a good time to seek out any potential township, county and state incentives.
As important as the design is the location of your facility. As more businesses are expanding their fulfillment operations and shipping directly to consumers, finding a facility close to your customers will help you design an optimal distribution network.
Finding the Right Facility
If you opt for an existing building, it is vital to design your operations to fit within that facility, or at least confirm it can indeed work in that particular space. Building dimensions and aspect ratio, ceiling height, bay spacing, and dock door locations and quantity are all critical factors to consider. In addition to accommodating your current design, it is also important to ensure the facility has the flexibility to adapt and grow as requirements change.
Building a new facility is a lengthier process and requires several additional steps. Once the detailed design is completed, the next step is selecting material handling equipment (MHE) vendors and identifying lead times. Depending on the specific MHE selected, these contracts may have to be executed immediately to ensure on-time arrival.
Moving to another facility is a big decision and long-term commitment. While in times of uncertainty it is impossible to predict the future, it is important to select a site that can accommodate flexible designs to ensure your operations are agile and resilient enough to meet the needs of the new-and next-normal.
A version of this article originally appeared in SupplyChainBrain.
How can we help improve your supply chain operations?
Schedule a consultation or contact Tompkins Solutions for more information.
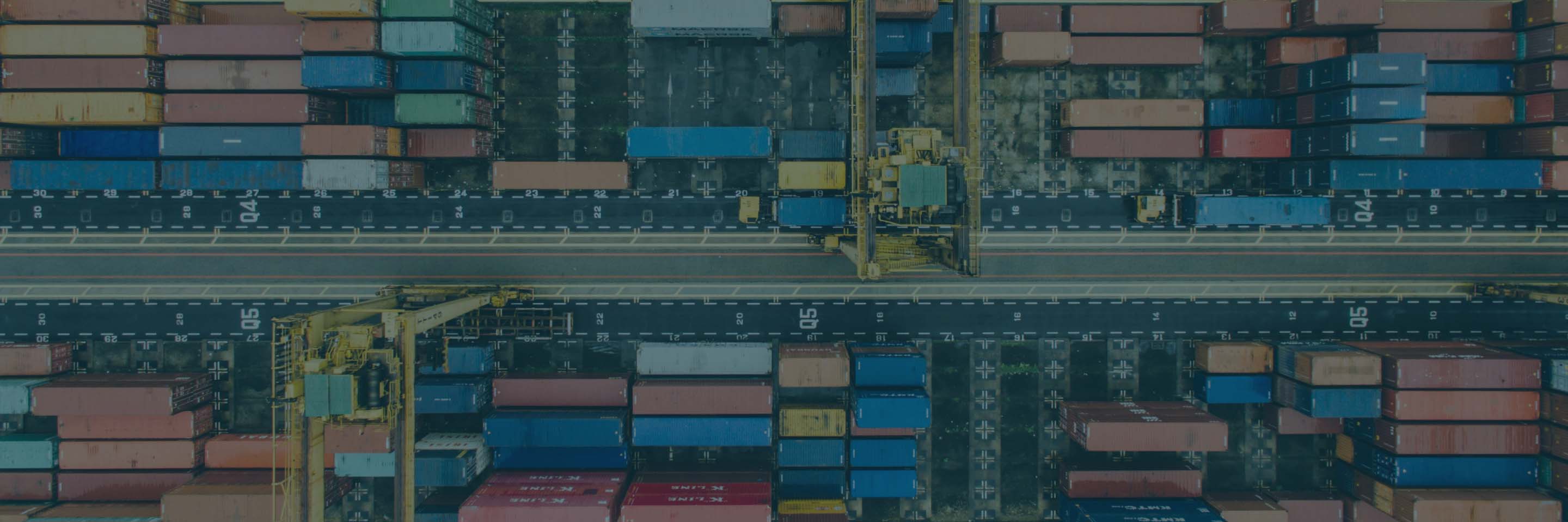
Featured Posts
Discover valuable resources to enhance your knowledge.