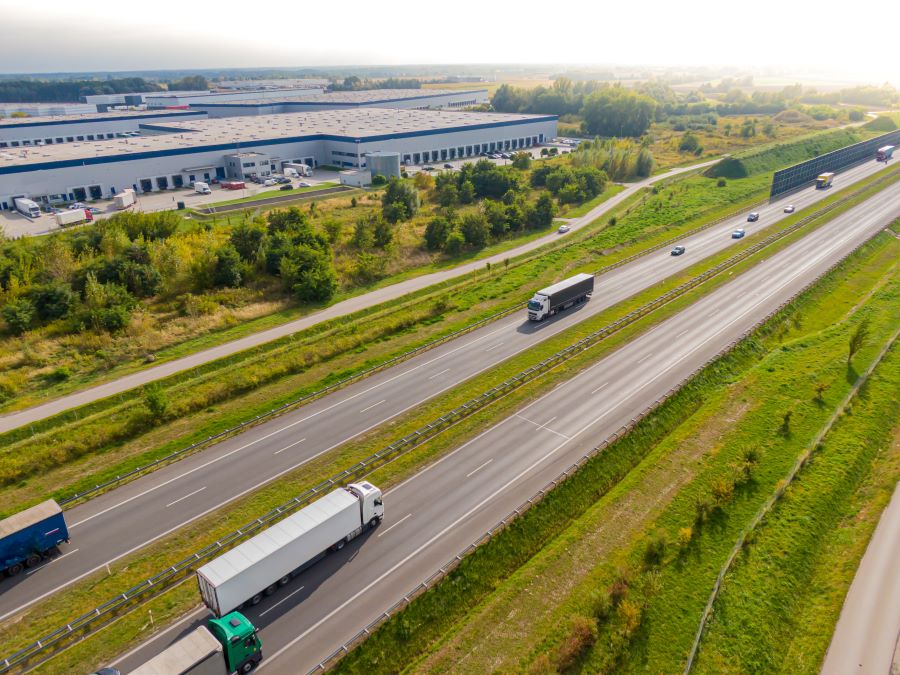
As disruptions continue to challenge supply chains worldwide, many companies may be looking at ways to increase the performance and resilience of their current network. An optimal supply chain network focuses on minimizing transportation and operations costs, maximizing profits and increasing service levels to customers. For some companies, this may mean expanding their distribution network.
Determining the optimal size, type, number and location of facilities requires careful planning and analysis. Below are five factors to consider before starting a distribution network optimization or expansion project.
Order and SKU profile and volume
With the changing retail landscape and rise of e-commerce sales, many distribution operations have gone from shipping large pallets of case quantities to retail stores to now shipping smaller orders with multiple SKUs directly to consumers. With e-commerce requiring more than three times the logistics space of traditional brick-and-mortar, shippers may need to redesign their logistics network and operations to accommodate the shift in shopping habits. Before considering expansion, it is important to clearly understand how adding facilities will impact your inventory and freight costs. Depending on your total SKU count, the additional inventory carrying costs may outweigh the reduction in transportation costs and times.
Current facility utilization
When looking to expand your network, it is important to first evaluate your current operations to identify any potential gaps, areas for improvement or opportunities to maximize your existing warehouse space. Companies should look at operations processes, layout, material flows, equipment and any other areas that can be enhanced to cut costs and increase efficiency, capacity and speed. This analysis can also help determine if automation is a viable solution to help optimize your current operations.
Expansion options
If after assessing your current facilities you determine expansion is necessary, the next step is identifying the best option to supplement your current network. Will you build a new facility from the ground up, retrofit a current facility, lease another existing facility or outsource part of your operations to a third-party logistics provider (3PL)? With warehouse demand and costs at an all-time high, companies with a robust retail store infrastructure can leverage these locations as micro-fulfillment hubs, offering ship-from-store fulfillment or buy online pick up in store (BOPIS). This method can also help companies reduce delivery times and costs.
Real estate and labor costs and availability
Demand and costs for warehouse space and labor have been consistently high over the last few years, with experts predicting these trends to continue into the near future. Even with Amazon reportedly unloading excess warehouse space, the industrial real estate market will continue to face low vacancy and high rental rates for the next two years, according to JLL. The warehouse labor market is facing similar woes, with Target recently raising its starting wage to up to $24 per hour depending on the local market. When evaluating potential locations, be sure to research the current real estate and labor rates and availability, as well as other competing organizations in the area. Additional factors, including unions, right-to-work laws and state and local incentives such as grants, rebates and tax credits, should also be considered during the location planning stage.
Transportation times and costs
Transportation is the most expensive part of logistics, accounting for anywhere from 50-70% of a company’s total logistics costs, according to CBRE. With shipping delays and costs continuing to rise, the location of your facilities and proximity to manufacturers, suppliers, retail stores and customers will play a vital role in driving down costs and achieving service level commitments. Utilizing a transportation management system (TMS) can provide visibility and insight to help companies select the best shipping option based on speed and cost.
While it may be tempting to act quickly to avoid future disruptions, a network optimization or expansion project is a massive undertaking that requires proper planning to ensure success. An experienced consultant can work with your company to conduct a network analysis and determine the optimal design capable of supporting your current and future requirements and long-term business objectives.
Contact us today to learn how to optimize your supply chain network to reduce costs, maximize profits and increase service levels to customers.
How can we help improve your supply chain operations?
Schedule a consultation or contact Tompkins Solutions for more information.
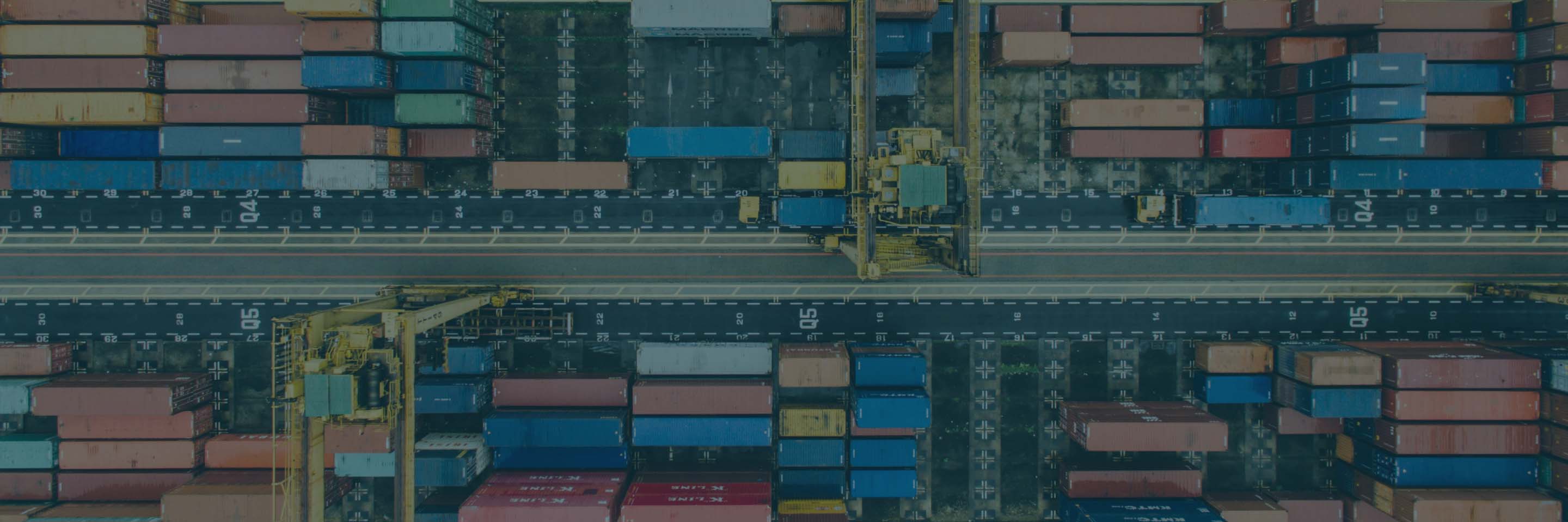
Featured Posts
Discover valuable resources to enhance your knowledge.