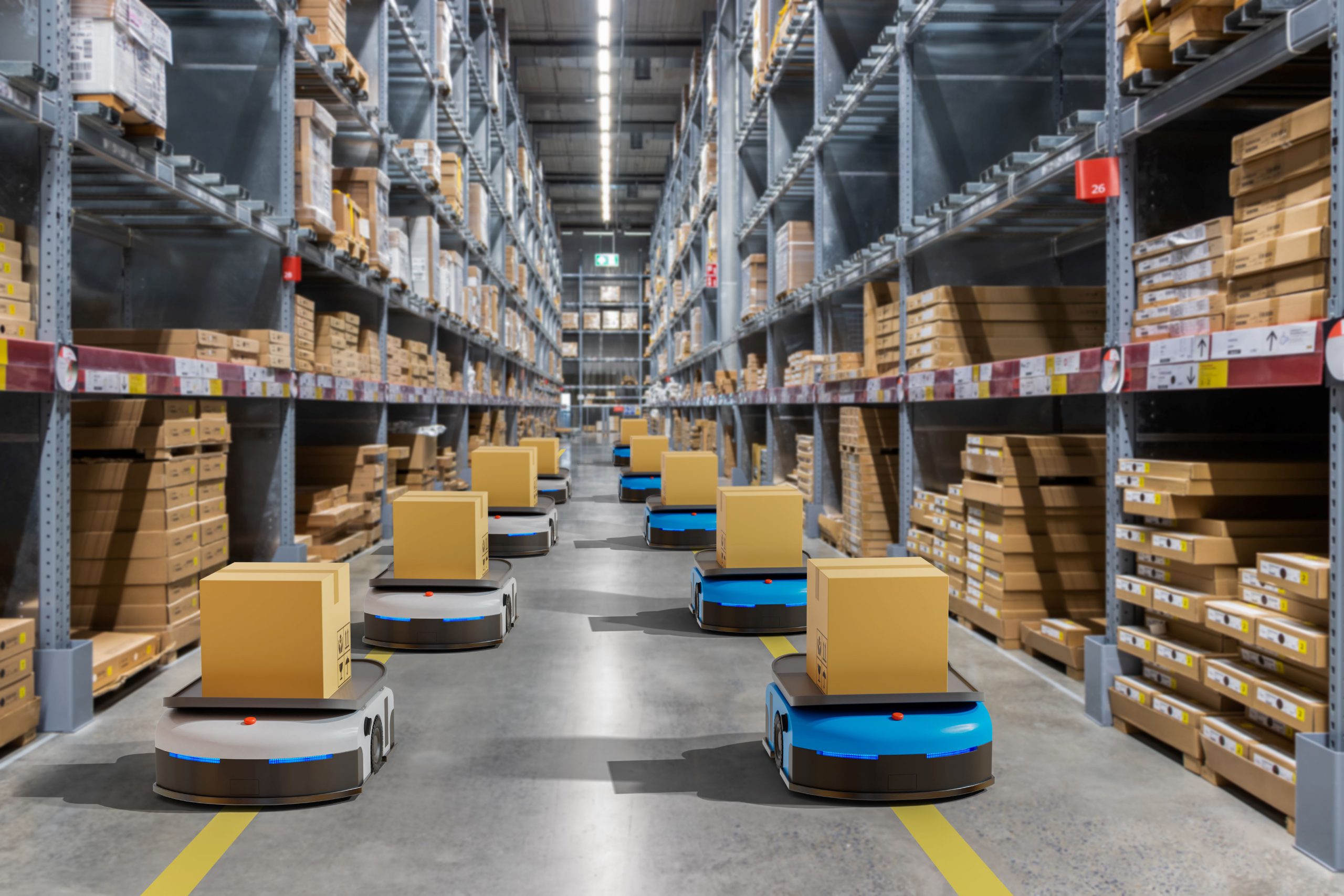
Automated Material Handling Systems
Implementing warehouse automation is unavoidable these days, as labor and space constraints continue to persist across logistics operations. Despite these realities, constantly changing demands, coupled with the large capital expense required for automation technology, some companies may still be hesitant to invest in automated material handling systems.
While the right type of warehouse automation will depend on your unique requirements and operations, many companies will benefit from the use of autonomous mobile robots (AMRs).
Benefits of Autonomous Mobile Robots
AMRs offer many benefits over traditional material handling equipment, including:
- Increased efficiency, accuracy and safety. AMRs assist humans by automating repetitive, labor and travel intensive processes, increasing speed and productivity. In addition to maximizing efficiency, AMRs utilize advanced navigation capabilities and sensors to reduce the risk of errors and injuries.
- Faster, easier installation. Since they don’t require extensive modifications to your existing infrastructure, AMRs can be set up in a fraction of the time of other material handling systems without interrupting your daily operations. And, with a fleet of AMRs in the facility, there is no single point of failure that shuts down operations.
- Maximum space utilization. Extending to storage solutions, some AMRs can help save cubic and picking space, creating more storage capacity in the same footprint while increasing the lifespan of the facility.
- Flexibility and scalability. AMRs can perform a wide variety of tasks, quickly adapt to changing requirements and be scaled up or down as needed to meet demand.
- Reduced costs. In addition to the cost savings achieved through the above benefits, AMRs require a lower upfront investment than traditional material handling systems, making them a more affordable and valuable option for many warehouse operations. AMRs are also very capital effective as you only need to purchase the quantity required at the time of deployment.
Warehouse Automation: Applications for AMRs
In addition to offering a multitude of advantages, AMRs can also be used in a wide range of functions throughout the warehouse, including:
- Picking. AMRs can assist with multiple picking methods, including delivering goods directly to pickers or by accompanying them throughout the warehouse to minimize travel time.
- Sortation. AMRs are capable of sorting items and packages for inbound or outbound logistics processes.
- Transportation. In addition to picking and sorting, AMRs can move parts, products and pallets over long distances throughout the warehouse.
- Inventory Management. RFID-enabled AMRs can automate inventory tracking to increase accuracy and visibility while freeing up labor for higher value tasks.
Steps for Selecting and Implementing Warehouse Automation
While AMRs offer a wide range of benefits and applications, it is important to determine what works best for your unique operations. Prior to selecting and implementing any warehouse automation solution, follow the steps below to ensure success.
- Establish objectives and collect data. Collect historical data, review existing operations and conduct interviews with key personnel to establish goals and priorities.
- Analyze data and define future operating requirements. Utilizing the data collected and the company’s growth projections, identify the functional requirements over the planning horizon. This analysis will also reveal any gaps or improvement opportunities in systems or operations.
- Evaluate potential solutions. Identify and evaluate automation options that address each gap and opportunity and meet the stated objectives. Develop a business case for each alternative with budgetary costs, improvement opportunities, estimated lead times and impact on operations and labor.
- Develop recommendations and an implementation roadmap. Develop a path forward strategy and implementation timeline for all major tasks associated with the recommended solution. The multi-year roadmap should sequence these efforts into manageable projects that balance ROI, speed to deploy, change management impact and budgetary constraints.
Learn more about the latest trends in warehouse automation.
While warehouse automation solutions can offer many benefits, they are not one-size-fits-all. With so many options on the market today, an experienced supply chain consulting firm can perform a strategic analysis, understand your business model and goals and help you select the best solution for your unique needs. Contact us today to get started on your warehouse automation project.
How can we help improve your supply chain operations?
Schedule a consultation or contact Tompkins Solutions for more information.
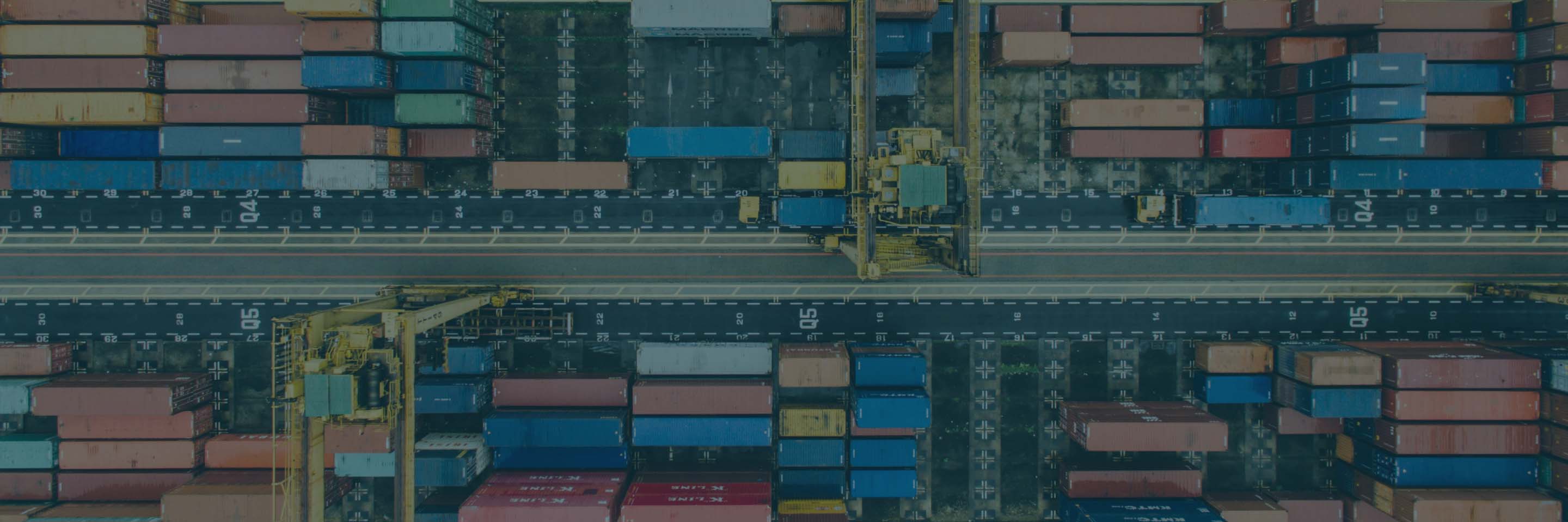
Featured Posts
Discover valuable resources to enhance your knowledge.