Warehouse Automation vs. Workforce Expansion: Which Solution is Right for Your Logistics Operations?
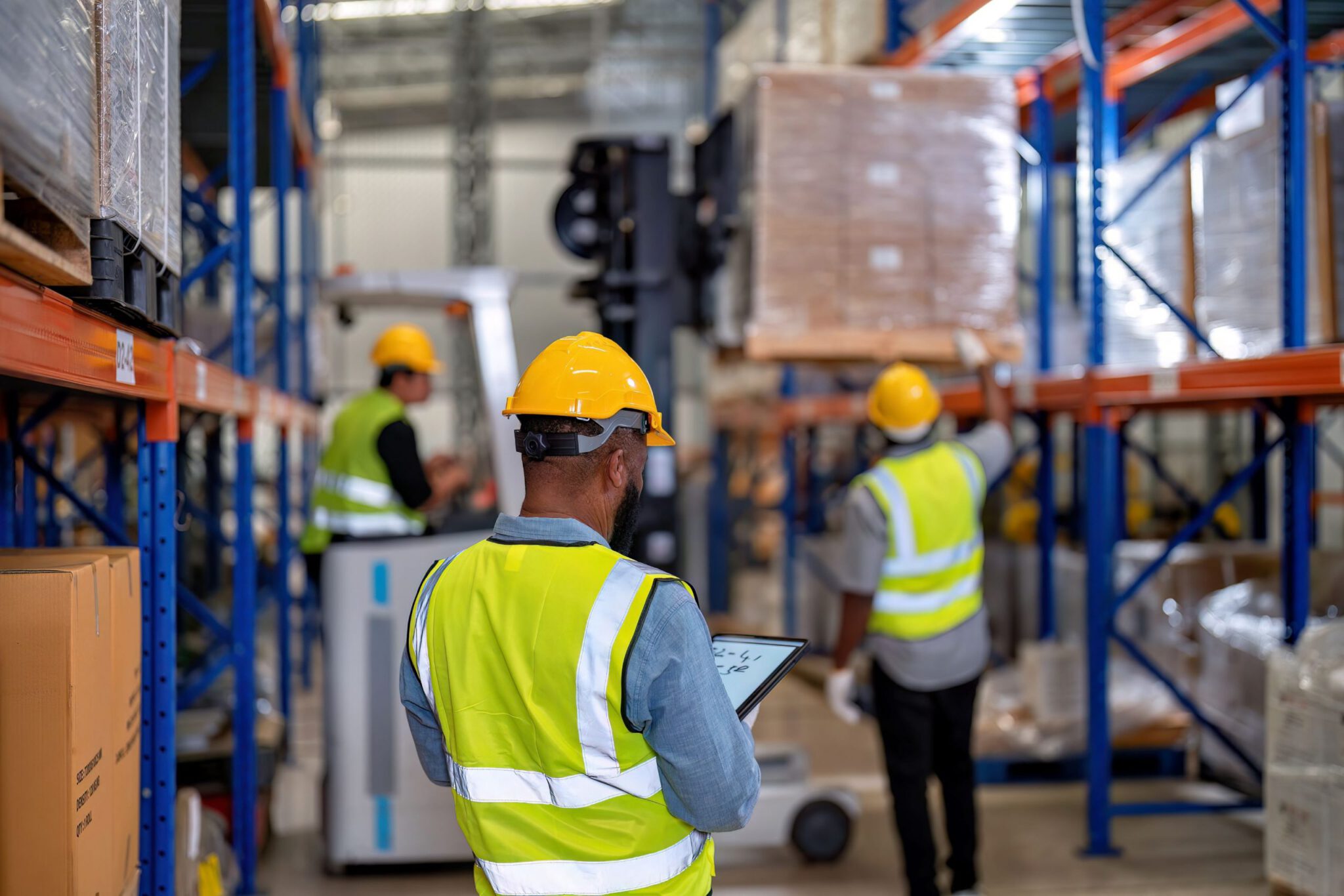
In today’s rapidly evolving landscape, logistics operations face the challenge of meeting increasing demands while remaining competitive. The decision to invest in automation or hire more workers is critical for long-term success. Each strategy comes with its own set of pros and cons, and the right solution will depend on each company’s unique requirements and operations.
Hiring More Workers
Pros:
- Greater Adaptability: Human workers possess the cognitive abilities and problem-solving skills required to handle changing tasks, unexpected challenges or irregularities in the logistics process.
- Easier Adoption: Hiring more workers is a straightforward solution that requires less data analysis and technical competency and is typically quicker to implement than automation.
Cons:
- Limited Scalability: Expanding the workforce to meet growing demands may be constrained by factors such as labor shortages, retention challenges and the need for physical space and infrastructure to accommodate additional employees.
- Human Error and Variability: Despite their capabilities, human workers are susceptible to errors, fatigue and variability in performance. This leads to inefficiencies, quality issues and delays in logistics operations.
- Increased Labor Costs: Hiring more workers entails ongoing expenses related to salaries, benefits, training and supervision. This significantly impacts operational costs, particularly in regions with high labor costs or stringent labor regulations.
To understand how manual labor fits into a modern warehouse strategy, explore Warehouse Automation: How to Select the Best Solution for Your Distribution and Fulfillment Operations.
Investing in Warehouse Automation
Pros:
- Increased Efficiency: Automated systems can perform repetitive tasks with precision and speed, leading to enhanced efficiency in various aspects of logistics operations, such as sorting, packaging and inventory management.
- 24/7 Operations: Unlike human workers who require breaks and rest periods, automated systems can operate continuously, enabling round-the-clock fulfillment of orders and minimizing delays in delivery schedules.
- Cost Savings: While the initial investment in automation technology may be significant, it can result in long-term cost savings by reducing the need for labor, minimizing errors and optimizing resource utilization.
- Increased Scalability: Automation solutions such as autonomous mobile robots (AMRs) can be easily scaled up or down and deployed across multiple sites to accommodate changing operational and market demands.
Cons:
- Initial Investment: Some automation solutions require a higher upfront investment in equipment, software, and infrastructure. Thus, it’s critical to weigh the payback period, initial capital investment and required volume to select the right solution for each situation.
- Technological Knowledge: Operating and maintaining automated systems require specialized skills and technical expertise, which may entail additional training for existing employees or hiring new personnel with relevant qualifications. However, the right solution can make onboarding new operators simpler than a manual process.
Learn more about automation technologies like AMRs and their applications in Warehouse Automation: Are AMRs the Right Solution for Your Logistics Operations?.
The Hybrid Approach
Many companies may find that a hybrid approach that combines automation and human labor can provide the best of both worlds. A gradual implementation strategy allows for scalability, while ongoing training and upskilling programs support the workforce’s evolution alongside technology. For example, a goods-to-person (GTP) solution can significantly minimize worker travel time and increase efficiency by bringing the items to be picked directly to the worker.
Prior to implementing a hybrid strategy, follow the steps below to determine the right combination of workers and automation solutions for your operations:
- Assess the specific needs and challenges of today’s operations
- Develop a targeted payback period, governed by an internal rate of return (IRR) or return on investment (ROI) calculation
- Review the company’s long-term growth goals
- Evaluate the initial capital investment and long-term cost implications and potential savings
- Find a partner that can deliver a modular, scalable and flexible solution
For guidance on navigating these considerations, visit 10 Trends in Warehouse Automation.
As distribution and fulfillment operations stand at the crossroads of automation and workforce expansion, a thoughtful and strategic decision-making process is essential. By carefully considering the advantages and challenges of each option, companies can navigate this decision successfully. Contact us today to learn how we can help you determine the right solution for your supply chain operations and increase resilience in this ever-changing logistics landscape.
How can we help improve your supply chain operations?
Schedule a consultation or contact Tompkins Solutions for more information.
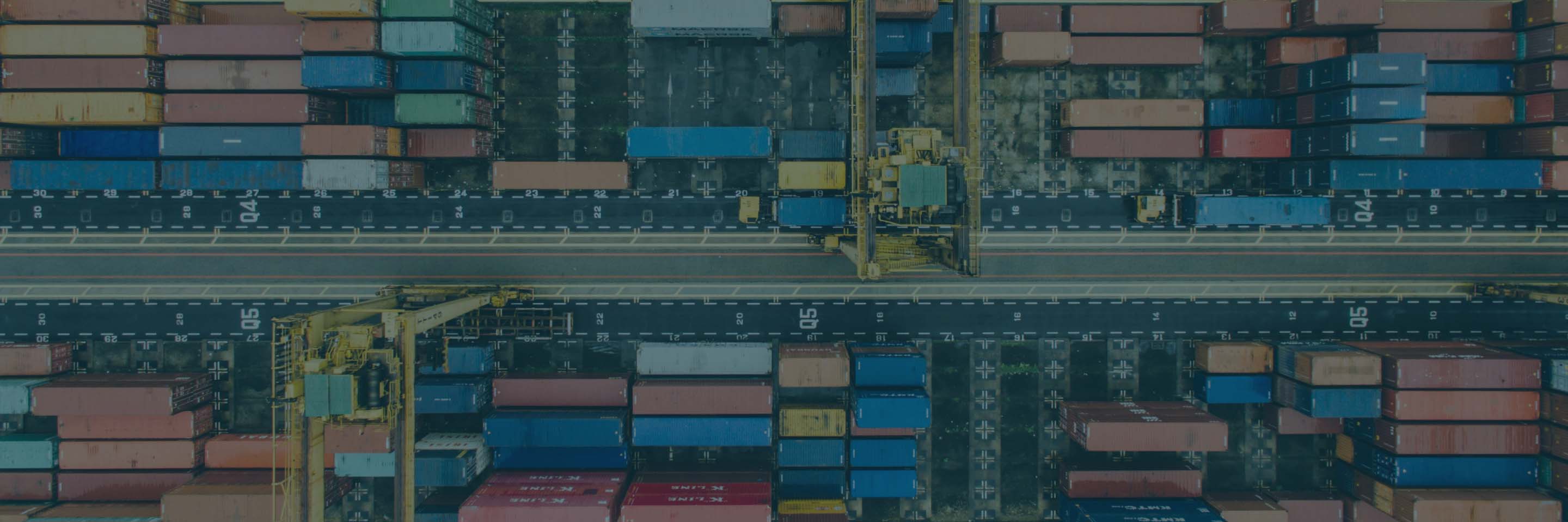
Featured Posts
Discover valuable resources to enhance your knowledge.