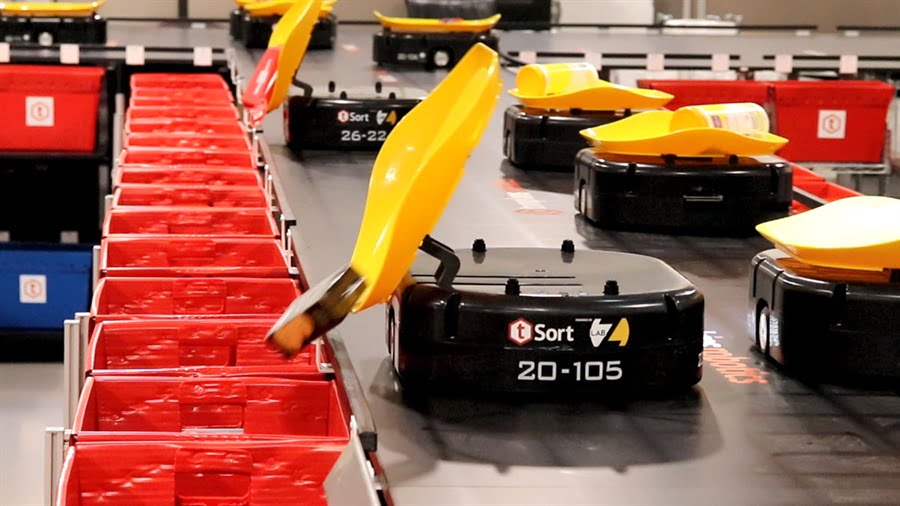
To satisfy customers, businesses need an operations strategy which stays in front of ever-changing consumer expectations. The key to an operations strategy is combining fulfillment and distribution into an integrated flow requiring more advanced capabilities in greater numbers of facilities. Fortunately, developments in robotics are providing opportunities to automate economically throughout the network. Picking solutions reduce operator travel and sorting solutions enabling all facilities to use more efficient batch pick and process flows.
Until recently, warehousing robots have been very limited in capability and prohibitive in cost. Today, feasible options exist for automating key processes even in small facilities. There are a number of notable solutions in picking and sorting.
Picking: Many remember the introduction of autonomous robotic solutions such as Amazon Robotics (formerly Kiva). This and other goods-to-person systems bring products to the picker in cases, totes, or entire shelves, then return the containers to a storage location. The pick and placement of items is directed and the operator works at a highly effective rate due to no travel, system direction, and the fast introduction and removal of goods and orders to process.
There are many versions of the goods-to-person systems available on the market. Some of the major players include Dematic, OPEX, SSI Schaefer, and AutoStore. AutoStore has a unique, high density storage design with robotic vehicles that operate on a grid above the storage system. This eliminates all aisles, while performing the putaway, retrieval, and movement functions.
Robot-enhanced picking provides a lower cost alternative to capital-intensive goods-to-person systems. Locus Robotics introduced a new approach to less-than-case fulfillment operations. The LocusBots work safely alongside human employees by positioning themselves at a pick location, providing pick instructions, and transporting full totes to sorting or packing.
Another trend is using robotic arms to perform the pick process, such as I Am Robotics and RightHand Robotics. These systems can detect, reach out, grasp, and place an item into a receptacle, fulfilling an order. "The supply chain of the future is more about pieces than pallets," according to RightHand Robotics, Co-Founder, Leif Jentoft.
Sortation: Automated sorting has historically been performed by tilt tray sorters, cross belt sorters, or other types of sorters that operate on a track, as opposed to independent robots. The exception has been automated guided vehicles (AGV) which for decades have been used for moving larger containers and pallets. t -Sort, a new technology developed by Tompkins Robotics and Lab Z uses the concept of a tilt tray, however the tilt tray is mounted atop a small AGV. t-Sort is an automated material handling sortation system that is creating a huge paradigm shift in the supply chain and how firms perform the basic distribution function of order fulfillment. These robots sort parcels to receptacles that are below or on the periphery of a mobile, linked tables or a light work platform. The system is more effective, costs much less, and can out-perform the fixed track sortation systems typically deployed in unit and parcel sortation oriented site. It also allows smaller firms to afford the type of automation that previously was out of reach financially.
Another example, Sure Sort, is a scalable, configurable, and cost-effective small item sorting system designed and manufactured by OPEX Corporation. Sure Sort is smart automation based on iBOT delivery technology; the same technology that drives the OPEX goods-to-person system.
Supply chain DC/FC performance is very sensitive to changes in business strategy and operating environments. To maintain a competitive advantage, the best companies have made automation a goal for ongoing DC/FC improvement to meet overall business objectives. Advancements in warehouse robotics have created new options for automating key processes in any facility.
Due to the speed of development, companies should regularly evaluate the feasibility of emerging robotic technologies.
How can we help improve your supply chain operations?
Schedule a consultation or contact Tompkins Solutions for more information.
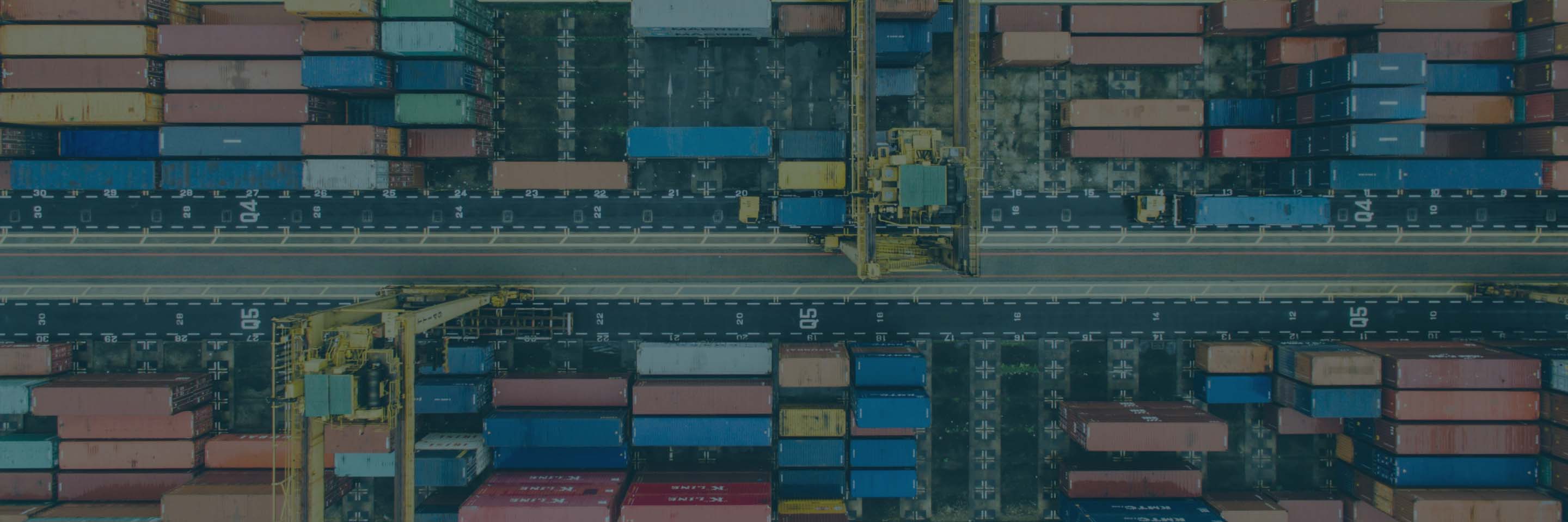
Featured Posts
Discover valuable resources to enhance your knowledge.