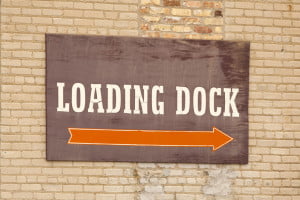
Updated 12/06/2024
The loading dock is one of the most dynamic areas in a warehouse, where goods flow in and out while heavy equipment and personnel interact in fast-paced environments. Dock safety is critical for protecting workers, reducing accidents, and maintaining efficient operations. Whether you are designing a new facility or enhancing an existing one, prioritizing dock safety in your warehouse design is essential for long-term success.
Common Dock Hazards
Dock accidents often stem from overlooked hazards, which can lead to severe injuries, damaged goods, and operational downtime. Some of the most common risks include:
- Truck Drive-Away: Trucks pulling away prematurely when drivers assume loading is complete.
- Trailer Creep: Gradual movement of trailers due to repeated forklift entry and exit.
- Water Hazards: Slip risks caused by rain, spills, or wet loads entering the dock area.
- Clutter: Empty pallets, packaging debris, and other materials creating trip hazards.
- Poor Visibility: Dim lighting obscuring personnel or the movement of goods.
- Falling Objects: Items dislodged during loading or unloading, endangering workers nearby.
Integrating safety considerations into your warehouse design can address these risks at the source, minimizing hazards before they arise.
Effective Dock Safety Measures
Minimizing dock hazards requires a combination of technology, processes, and best practices tailored to your operation. Consider implementing these proven solutions as part of your warehouse design or retrofitting process:
1. Truck Restraints
Prevent truck drive-away and trailer creep with robust restraint systems. Options range from simple wheel chocks to fully automated trailer restraints with visual indicators. Enhancements like handles and flags improve visibility, while clamps on trailer wheels or underrun bars add stability.
- Pro Tip: Use restraint status lights to signal drivers and loaders when it’s safe to proceed.
2. Dock Levelers
Bridge the gap between trailers and docks while compensating for height variations during loading and unloading. Modern dock levelers improve efficiency and reduce worker strain. Including these systems in warehouse design ensures seamless operations and reduces manual effort.
Example:
A national grocery chain implemented dock levelers in its cold storage distribution centers to handle frequent height variations caused by temperature-controlled trailers. The dock levelers ensured a smooth transition for forklifts and pallet jacks, preventing product damage and reducing strain on workers. This upgrade minimized delays, improved safety, and allowed the facility to maintain faster turnaround times for deliveries.
3. Dock Seals and Canopies
Prevent water and debris from entering the dock area, reducing slip hazards and keeping the workspace clean and dry. These features can be incorporated into initial warehouse design to promote a safer, weather-resistant environment.
Example:
In a high-volume retail distribution center, dock seals and canopies were installed to ensure uninterrupted operations during rainy seasons. By preventing water ingress, the facility significantly reduced slip hazards for workers unloading pallets and maintained the integrity of packaged goods, avoiding costly damage. This small investment helped the retailer improve both safety and operational efficiency.
4. Improved Lighting
Equip forklifts and dock areas with high-intensity lights to enhance visibility, making it easier to identify personnel and safely handle loads. Lighting plays a critical role in accident prevention, especially in dimly lit areas where personnel and goods are frequently in motion. Incorporating strategically placed lights as part of your warehouse design improves safety and boosts operational efficiency.
5. Netting and Barriers
Install netting on elevated loading conveyors and designate pedestrian-only zones near docks. These measures protect against falling objects and reduce worker injuries. Including barriers in your warehouse design layout creates a safer flow of traffic throughout the facility and minimizes risks to employees in high-activity areas.
6. General Housekeeping
Adopt a proactive approach to cleanliness:
- Remove clutter and debris immediately.
- Organize pallets and packaging materials.
- Sweep and mop regularly to minimize hazards.
Designating specific zones for debris disposal and cleaning tools as part of your warehouse design encourages consistent upkeep and a safer working environment.
7. Practical Processes
Small procedural changes can have a significant impact:
- Collect driver keys upon check-in and hold them during loading or unloading.
- Use clear signage to guide personnel and truck drivers through the dock area.
Implementing these practices not only reduces risks but also ensures a smoother flow of operations at busy docks.
Warehouse Automation for Dock Loading
Integrating warehouse automation with dock loading operations can significantly enhance safety, accuracy, and efficiency. Some key automation technologies include:
- Automated Guided Vehicles (AGVs): These driverless machines can transport pallets and goods between trailers and staging areas, reducing the risk of accidents and manual labor requirements.
- Conveyor Systems with Load Sensors: Advanced conveyor systems equipped with load sensors can automatically move goods to the correct location while monitoring weight and balance to prevent overloading.
- Robotic Arms for Loading and Unloading: Robotic systems can perform repetitive tasks like loading pallets into trailers, ensuring consistent operations while minimizing worker fatigue.
- Dock Scheduling Software: Automates the coordination of truck arrivals, preventing congestion and ensuring docks are utilized efficiently.
- Vision Systems and AI Monitoring: Cameras and AI-powered analytics can monitor dock activity in real time, identifying hazards or inefficiencies and alerting operators to potential issues.
Incorporating these technologies into your warehouse design not only enhances safety but also boosts productivity and minimizes operational delays.
Warehouse Design for Safety
At Tompkins Solutions, we recognize that effective warehouse design goes beyond space utilization—it’s about creating a safe, efficient, and future-ready environment. Whether planning a new facility or optimizing an existing one, incorporating dock safety measures into the design phase helps prevent hazards and streamlines operations.
From strategic dock placement to selecting the right equipment and automation technologies, a safety-focused warehouse design lays the foundation for long-term operational success.
How can we help improve your supply chain operations?
Schedule a consultation or contact Tompkins Solutions for more information.
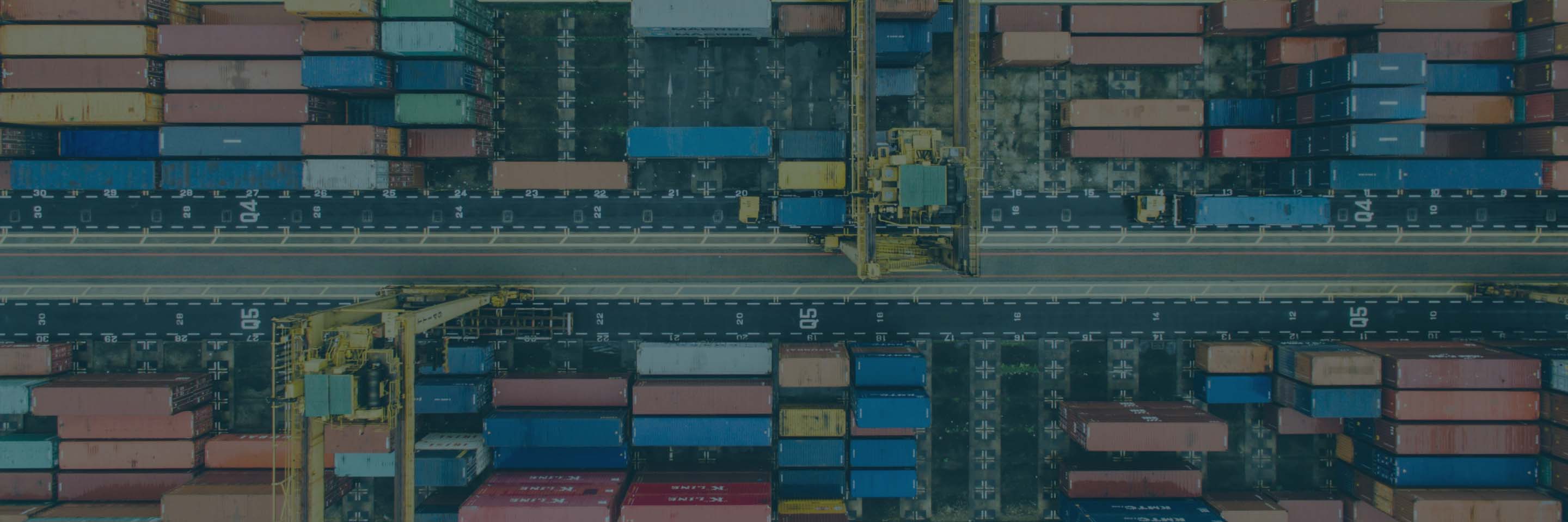
Featured Posts
Discover valuable resources to enhance your knowledge.