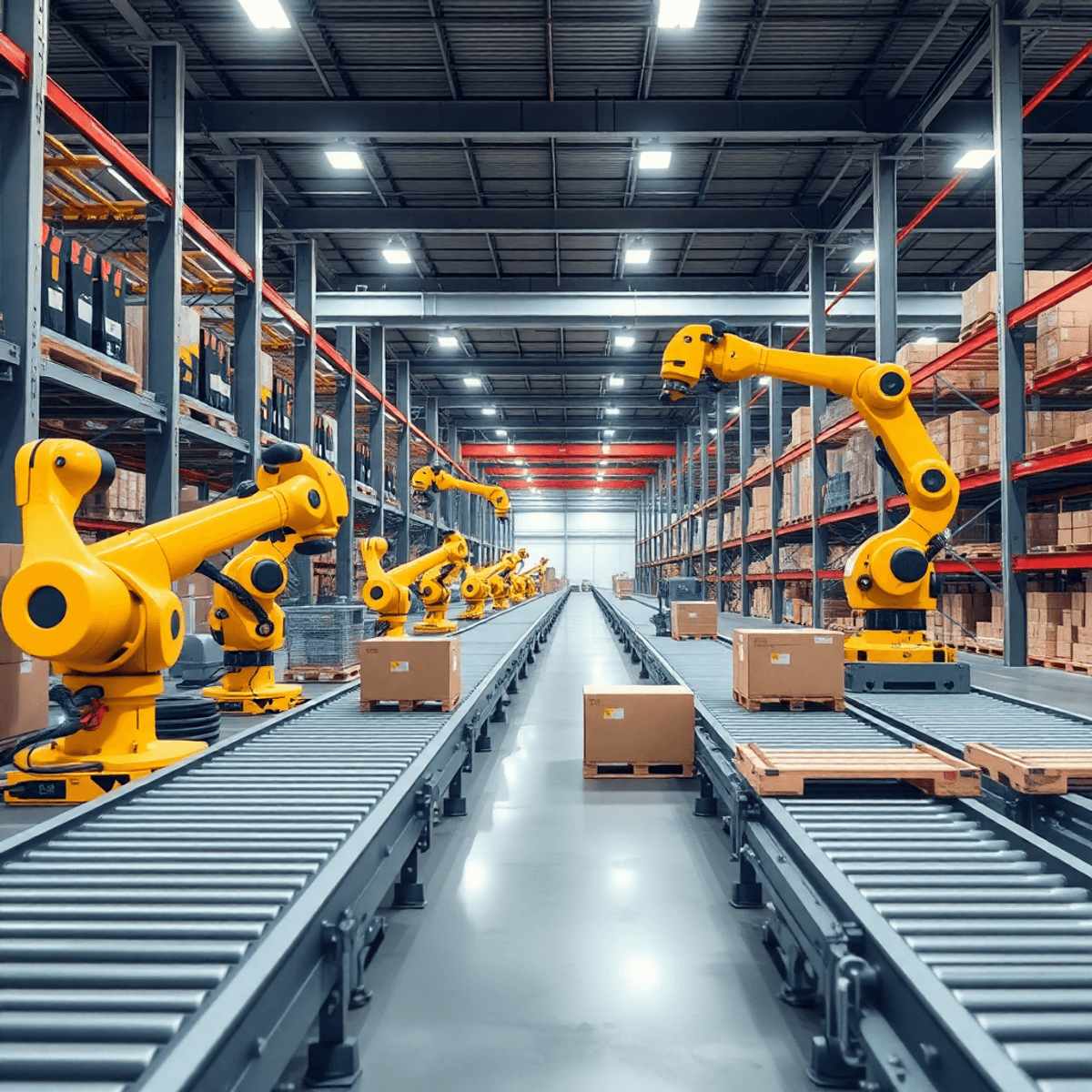
Mastering Warehouse Operations with Automated Material Handling Equipment
Automation in modern warehouses is no longer a luxury but a necessity. Automated Material Handling Systems (AMHS) play a critical role in optimizing warehouse operations by enhancing efficiency and reducing labor requirements through robotic material handling. This transformation is driven by technologies such as automated material handling conveyors and automated material handling equipment that streamline the transportation, sorting, and storage processes.
However, the successful implementation of these systems requires careful planning and execution. For instance, understanding the do's and don'ts for a material handling equipment installation can significantly enhance your operational performance.
Moreover, with the advent of Autonomous Mobile Robots (AMRs), warehouse automation has taken a new turn. AMRs optimize warehouse operations with improved efficiency, scalability, cost savings, and applications like picking and inventory management.
In addition, selecting the right sorter for your material handling automation system is crucial. Our guide on how to choose the right sorter provides valuable insights into this process.
Embracing these innovations not only boosts operational performance but also provides a competitive edge in the rapidly evolving market landscape. Investing in an automatic material handling system can revolutionize your warehouse operations, setting you on the path to success.
Understanding Automated Material Handling Systems (AMHS)
Automated Material Handling Systems (AMHS) are a cornerstone of modern warehouse operations. By automating the movement, sorting, and storage of materials, these systems enhance efficiency and reduce labor demands. At the heart of AMHS are various components that work in tandem to streamline processes.
1. Conveyor Systems
Conveyor systems are crucial for transporting goods within a warehouse. They come in different types, each designed for specific tasks:
- Belt Conveyors: Best for moving items over long distances, especially bulk materials or packaged products.
- Roller Conveyors: Suitable for heavier items or those with a flat bottom, using rollers to facilitate movement.
- Accumulating Conveyors: Allowing temporary storage and controlled release of products, useful in buffering processes.
- Vertical Conveyors: Optimizing space by transporting goods vertically between different levels.
Recent advancements in conveyor technology focus on enhancing efficiency and flexibility:
- Smart Control Systems: Using sensors and automation to optimize the flow of goods based on load requirements.
- Energy Efficiency: Reducing energy consumption through energy-efficient motors and regenerative braking systems.
- Modular Designs: Featuring components that can be easily reconfigured to adapt to changing operational needs.
The integration of automated conveyors within AMHS not only streamlines material handling but also improves safety by reducing manual interactions. As warehouses strive to meet increasing demands with precision and speed, automated conveyor systems play an indispensable role in transforming traditional operations into efficient hubs.
Conveyor systems form just one aspect of the broader AMHS landscape, yet their impact on warehouse efficiency is substantial. Understanding these components provides a foundation for exploring other automated solutions that collectively revolutionize warehouse operations. For instance, learning about conveyor system selection can further enhance understanding and implementation of these critical systems in warehousing.
2. Automated Guided Vehicles (AGVs)
Automated Guided Vehicles (AGVs) play a crucial role in today's Automated Material Handling Systems (AMHS), improving the speed and accuracy of warehouse operations. These vehicles move around the warehouse on their own, making it easier to transport materials and reducing the need for manual labor and human mistakes.
Key Benefits of AGVs:
- Improved Efficiency: AGVs facilitate the seamless transportation of goods, optimizing traffic flow within the warehouse.
- Enhanced Safety: With onboard sensors and advanced navigation systems, these vehicles minimize the risk of accidents during material handling.
- Cost Reduction: Over time, AGVs can reduce operational costs by replacing manual labor and decreasing error-related expenses.
Types of AGVs:
- Pallet Handling Robots: Designed for transporting pallets, these AGVs efficiently move heavy loads across large distances within a warehouse.
- Pick-Assist Robots: These enhance order fulfillment tasks by assisting human workers in picking processes, thereby increasing speed and accuracy.
AGVs are a significant advancement in automated material handling, making warehouses smarter and more adaptable.
3. Robotic Systems
Robotic systems are crucial for improving both speed and accuracy in warehouse operations. These systems automate tasks that were typically done by human workers, leading to quicker processing times and fewer mistakes. By using robotic arms with advanced sensors and software, warehouses can greatly improve their picking, packing, and sorting activities.
Automated Storage and Retrieval Systems (AS/RS)
Automated Storage and Retrieval Systems (AS/RS) are vital for optimizing space usage in warehouses. These systems employ robotic mechanisms to efficiently move items in and out of storage areas. By making the most of vertical space and reducing the width of aisles needed, AS/RS enable denser storage solutions, which is especially advantageous in places where space is limited.
Pros and Cons when Implementing your AMHS
Implementing Automated Material Handling Systems (AMHS) offers significant advantages to warehouse operations:
Benefits of Implementing AMHS
- Increased Operational Efficiency: Streamlined processes within AMHS reduce the time spent on manual tasks, allowing for faster movement of goods and increasing throughput. By automating repetitive tasks, warehouses can operate more smoothly and efficiently.
- Improved Safety: By minimizing manual handling tasks, AMHS significantly reduces the risk of injuries associated with lifting, pushing, or pulling heavy loads. This not only ensures a safer working environment but also helps in reducing costs related to workplace accidents.
- Enhanced Order Fulfillment Accuracy: With automation, the likelihood of human error is greatly diminished. This leads to improved accuracy in order picking and fulfillment, directly contributing to higher customer satisfaction levels.
Moreover, warehouse automation boosts dock efficiency with better storage, faster picking, improved safety, and reduced labor costs.
Challenges of Implementing AMHS
- High Initial Investment Costs: The upfront costs associated with acquiring and integrating AMHS can be substantial. Businesses must carefully consider their budget and potential return on investment (ROI) when planning implementation.
- Integration Complexities: Integrating AMHS with existing systems can be complex. Ensuring seamless communication between new technologies and current infrastructure requires thorough planning and possibly significant adjustments to existing workflows.
Understanding these factors is crucial for any business considering the adoption of AMHS to make informed decisions that align with their operational goals.
Advanced Systems Shaping the Future of Material Handling
1. Robotic Picking Systems
The integration of robotic picking systems in warehouses has significantly enhanced both speed and accuracy in picking processes. These systems, equipped with advanced vision technologies, allow for precise item selection, reducing human error and labor costs. By automating this critical task, warehouses can handle larger volumes of orders more efficiently, improving overall productivity and customer satisfaction.
2. Sortation Systems
Efficient routing of items through sortation systems is another technological advancement driving automation in modern warehouses. These systems classify and direct products based on specific supply chain criteria using methods like cross-belt sorters or robotic sortation solutions. This automation reduces bottlenecks in material flow and ensures timely order processing, essential for meeting consumer demands.
3. Palletizing Systems
In the realm of shipping and logistics, palletizing systems play a pivotal role in stacking goods effectively for transport. Automated palletizers streamline the packaging process by arranging products in optimal configurations on pallets. This not only maximizes space utilization within shipping containers but also minimizes damage during transit, contributing to a more reliable supply chain.
These emerging technologies underscore the transformative potential of automated material handling solutions across various facets of warehouse operations. To fully leverage these advancements, it's crucial to consider warehouse design as it plays a significant role in optimizing the overall efficiency of material handling processes.
Software Integration Considerations for your AMHS
Software integration is crucial for fully utilizing Automated Material Handling Systems (AMHS). Warehouse Management Systems (WMS) and Warehouse Control Systems (WCS) are key players in this process.
Warehouse Management Systems (WMS)
These systems are essential for optimizing inventory management. They provide real-time visibility into stock levels, locations, and movements, ensuring that the right products are available at the right time. By coordinating tasks like picking, packing, and shipping, WMS streamlines warehouse operations, reducing errors and enhancing productivity.
Warehouse Control Systems (WCS)
While WMS focuses on overarching inventory management, WCS manages the operational aspects of material handling equipment. It directs the flow of materials within the warehouse, ensuring that conveyors, AGVs, and robotic systems operate efficiently. This coordination minimizes downtime and maximizes throughput.
The collaboration between WMS and WCS creates a smooth operation where both strategic planning and tactical execution work together. This integration not only improves efficiency but also allows for scalability to meet growing business demands. By using these software solutions, warehouses can achieve higher accuracy in order fulfillment and improved customer satisfaction.
Future Trends in Automated Material Handling Solutions
The world of automated material handling solutions is changing quickly, with sustainability and flexibility becoming important themes.
Sustainability
More and more, businesses are incorporating sustainable practices into their material handling solutions. This change is driven by both environmental responsibility and economic efficiency. Here's what you can expect:
- Energy-efficient technologies, such as low-power conveyors and solar-powered systems, are gaining popularity.
- Manufacturers are focusing on using recyclable materials and reducing waste through more precise automation techniques.
Flexible Automation
As business needs change, so does the demand for adaptable solutions. Flexible automation allows warehouses to adjust quickly to changes in demand or shifts in product lines. Here's how this trend is shaping up:
- Modular systems that can be easily reconfigured or expanded are becoming essential.
- Technologies like robotic arms with interchangeable tools or AGVs with adaptive navigation capabilities exemplify this trend, offering the ability to respond dynamically to new challenges without extensive downtime or restructuring.
Both trends show a larger movement towards making warehouse operations future-proof, ensuring they stay competitive and resilient in a constantly changing market. As these technologies continue to develop, they promise not only improved efficiency but also a smaller impact on the environment and greater ability to adapt to market demands.
Embracing Automation for Competitive Advantage in Warehouse Operations
Automated Material Handling (AMH) is a game-changer for mastering warehouse operations. This technology has the power to transform businesses by improving efficiency, accuracy, and safety, giving them an edge over competitors. By using AMH solutions, companies can not only keep up with their rivals but also surpass them.
Explore further resources and consult with industry experts to dive deeper into your automation journey. Embrace these advancements to unlock new levels of operational excellence and secure your foothold in an ever-evolving market.
FAQs (Frequently Asked Questions)
What is Automated Material Handling Equipment and why is it important?
Automated Material Handling Equipment (AMHE) refers to the technology used to automate the movement, protection, storage, and control of materials within a warehouse. Its importance lies in its ability to revolutionize warehouse operations by increasing efficiency, reducing manual labor, enhancing safety, and improving order fulfillment accuracy.
What are the key components of an Automated Material Handling System (AMHS)?
Key components of an AMHS include conveyor systems, Automated Guided Vehicles (AGVs), and robotic systems. These components work together to optimize warehouse processes, streamline material flow, and enhance operational efficiency.
What types of conveyor systems are commonly used in warehouses?
Common types of conveyor systems used in warehouses include belt conveyors, roller conveyors, and accumulating conveyors. Each type has specific applications that cater to different material handling needs, contributing to improved efficiency in warehouse operations.
What benefits do Automated Guided Vehicles (AGVs) provide in warehouse settings?
AGVs enhance material flow within warehouses by automating the transportation of goods. Their functionality includes pallet handling and pick-assist capabilities, which streamline processes and reduce the risk of human error.
How can we help improve your supply chain operations?
Schedule a consultation or contact Tompkins Solutions for more information.
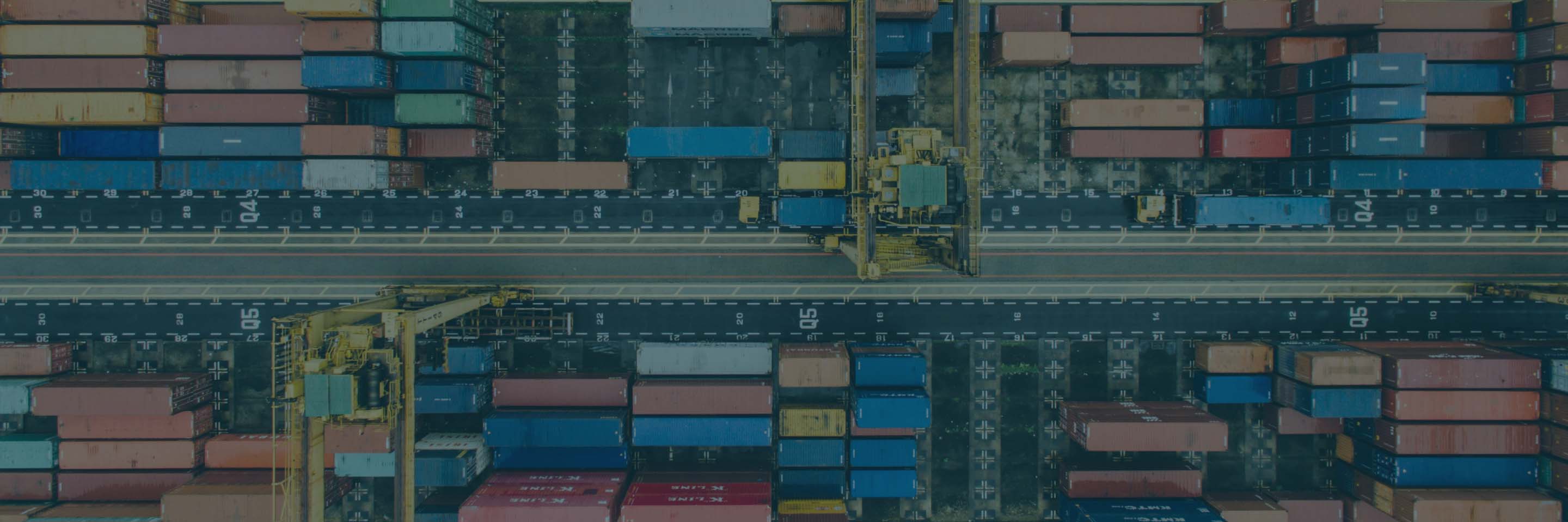
Featured Posts
Discover valuable resources to enhance your knowledge.