This updated article enhances the original content by restructuring for improved readability, adding explicit solution sections for each implementation pitfall, and introducing a new educational section on the warehouse technology stack (WMS, WCS, WES). The additions provide crucial context about system differences and why understanding these distinctions prevents common implementation failures when defining requirements with vendors.
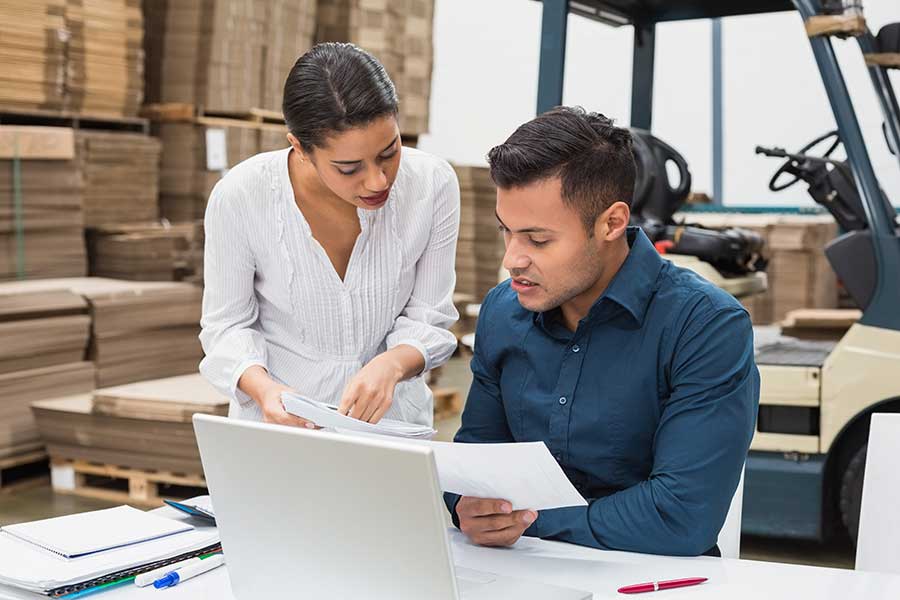
Navigating Warehouse Management System Implementation Challenges
Many warehouse management system (WMS) implementations underperform. They overrun budgets, blow out schedules, fail to deliver promised results and inflict excessive go-live pain. In all fairness to WMS deployments, other business system implementations can fall short too. But as an operations-centric execution system, a WMS deployment is very susceptible to a wide variety of pitfalls that can result in poor project results and potentially a failed implementation.
The shape and magnitude of these pitfalls vary according to each WMS implementation's size, complexity, business requirements and drivers. While implementations backed by strong project management functions are generally well equipped to deal with these potential hazards, they are not immune to underperforming because of them. Understanding how to avoid or mitigate the potential landmines can make or break a warehouse management system implementation.
Implementation pitfalls can be categorized and analyzed in various ways. Below are four planning challenges that can negatively impact your WMS implementation, as well as solutions for dealing with each pitfall.
Understanding the Warehouse Technology Stack
Before diving into common implementation pitfalls, it's crucial to understand the different systems that make up the modern warehouse technology stack. Many implementation challenges stem from confusion about the roles and responsibilities of each system.
WMS, WCS, and WES: Clarifying the Differences
Warehouse Management System (WMS) focuses on inventory management and orchestration of warehouse operations. It handles receiving, putaway, inventory tracking, order allocation, picking, packing, shipping, and labor management. A WMS is the strategic brain of the warehouse, determining what work should be done and when.
Warehouse Control System (WCS) manages and directs the real-time activities of warehouse automation equipment such as conveyors, sorters, AS/RS systems, and pick-to-light systems. The WCS is the tactical component that translates the WMS's instructions into specific commands for automation equipment.
Warehouse Execution System (WES) bridges the gap between WMS and WCS, optimizing the flow of work by synchronizing and sequencing tasks across labor and automation resources. A WES provides real-time decision-making capabilities to balance workloads and prioritize activities, especially in environments with complex automation.
For a deeper dive into the world of Warehouse Management Systems check out our Beyond the Barcode episode with Softeon's Mark Fralick.
Why Understanding the Stack Matters for Requirements Definition
Understanding these distinctions is vital when defining requirements with vendors for several reasons:
- Proper Functionality Allocation: Clearly defining which functions belong to which system prevents capability gaps or unnecessary overlaps that can lead to implementation issues.
- Integration Complexity: Each interface between systems adds complexity and potential points of failure. Understanding the technology stack helps in planning appropriate integration strategies.
- Performance Expectations: Each system has different processing capabilities and response time expectations. WCS systems typically require sub-second response times, while WMS systems may operate on longer cycles.
- Vendor Selection: Some vendors offer comprehensive solutions spanning multiple layers, while others specialize in one area. Understanding your stack helps determine whether a best-of-breed or integrated approach is more appropriate.
- Future Scalability: As operations grow or automation is added, understanding how each component scales and evolves prevents costly rework.
When stakeholders don't understand these distinctions, they may place inappropriate requirements on the wrong system, leading to custom development, performance issues, or failed implementations. Establishing a clear technology blueprint before engaging vendors helps ensure realistic expectations and appropriate system design.
Common Warehouse Management System Implementation Pitfalls
The Job is Bigger than Expected
This is probably the most common reason that WMS implementation projects flounder. The schedule, resource requirements and budget set when the project was approved turn out to be inadequate. This can be due to a variety of factors:
- Participants in a WMS selection and approval process (operations, IT, software vendor, integrator, etc.) may have been overly optimistic when determining resource requirements and the timeline
- Since they probably wanted the project to proceed, they consciously or subconsciously tried to accommodate perceived budgetary thresholds and schedule goals
- A WMS design process is typically an iterative proposition requiring layer-by-layer analysis
- Selection requirements typically only represent the first layer, with many unknowns buried in underlying layers that impact schedule, budget and resource requirements
Solution: The best approach is to avoid this pitfall by conducting thorough due diligence during the selection and approval process. This should include:
- A critical review of each bidder's proposed project plan and resource estimates
- Direct discussion on contingencies the vendor or integrator has included to cover unknowns
- Ensuring your own responsibilities are adequately defined with appropriate contingencies, especially for setup, facility preparation and testing
If you find yourself with insufficient resources despite preventative measures:
- Address the issue immediately—bad news will not improve over time
- If the established schedule and budget are inflexible, determine what functionality can be deferred to a subsequent phase
- Continuing without directly addressing the shortfall will not turn out well
Misaligned and Hidden Requirements
Most WMS implementations depend on a detailed design process to deliver the required functionality and features. During this process, the WMS vendor or systems integrator develops design documentation and specifications through observations, workshops and reviews with client stakeholders and subject matter experts (SMEs).
The challenge here is that team members often see things differently due to varying perspectives and project roles. It's easy to assume everyone involved in designing a particular process is aligned when significant misalignment exists on how the system should work. Words—even when backed up by flow diagrams—can be interpreted differently by the people involved.
This tendency is compounded when an operation has many requirements that exist outside documented standard operating procedures. These hidden requirements may not be fully articulated because they seem obvious or get lost in the shuffle.
Solution: The best remedy is frequent playback sessions where relevant processes and features are reviewed end-to-end, from design approval through delivery. These sessions will help discover any misalignment between the vendor/integrator and client stakeholders/SMEs so issues can be addressed efficiently.
Too Little or Too Much Thinking Outside of the Box
Client stakeholders and SMEs have a natural tendency to view requirements through the lens of how things work today. This can result in missed opportunities to increase operational efficiencies and improve service levels.
Conversely, stakeholders might propose ideas they believe will significantly improve operational performance, but which drive complexity and effort into the deployment, jeopardizing schedule and budget. There may be alternatives closer to base WMS functionality that can provide 85%+ of the benefits at a fraction of the risk and cost.
Additionally, stakeholders often push to include every piece of functionality they think might eventually be useful, assuming that if they don't get it now, they never will. This can lead to a detailed design that far exceeds the original budget.
Solution: Open, direct communications are vital:
- Client stakeholders and SMEs should be consistently challenged to consider better ways of doing things
- Vendors and integrators need to be encouraged to push back when they believe a specific process adds unwarranted complexity and risk
- Project management must ensure all parties feel comfortable speaking their minds
Project Plans that Fail to Deliver Value
Behind every WMS implementation is some form of project plan, but these plans don't always live up to their potential. They may become unwieldy tools that consume too much effort for the value produced.
Many implementations approach the project plan as a glorified activities list with little consideration for resource requirements. Tasks are viewed as strictly linear when they may need to reflect a more iterative process. This can result in a project plan that delivers diminishing value over the project lifecycle, with too much time spent inventorying individual tasks instead of assessing overall project health.
Solution: Developing a well-structured plan is key to avoiding this pitfall:
- When appropriate, summarize instead of detailing
- Many detailed activities are better managed through punch lists by the responsible workstream
- The plan structure should be adaptable to changing conditions and insights
- The structure should support an earned value measurement mechanism for monitoring budgetary performance beyond perceived duration
- Focus weekly project status meetings on the health of various project sections rather than the status of individual tasks
The Path Ahead
Successfully implementing a warehouse management system requires careful planning, clear requirements definition, and strong project management. By understanding the key technology components in your warehouse stack and avoiding the common pitfalls outlined in this article, you can significantly increase your chances of a smooth implementation that delivers on its promised value.
Remember that the most successful implementations begin with thorough preparation, realistic timelines, and appropriate contingencies. They're characterized by open communication, regular playback sessions, and the willingness to challenge assumptions from all stakeholders.
Need Expert Guidance?
Navigating the complexities of WMS selection and implementation can be challenging. If you're planning a warehouse management system project or experiencing challenges with your current implementation, Tompkins Solutions specialists can help. Our experienced team has guided hundreds of successful WMS implementations across various industries and complexity levels.
Contact a Tompkins Solutions specialist today to discuss your warehouse technology needs and ensure your WMS implementation delivers the operational excellence and ROI you expect.
How can we help improve your supply chain operations?
Schedule a consultation or contact Tompkins Solutions for more information.
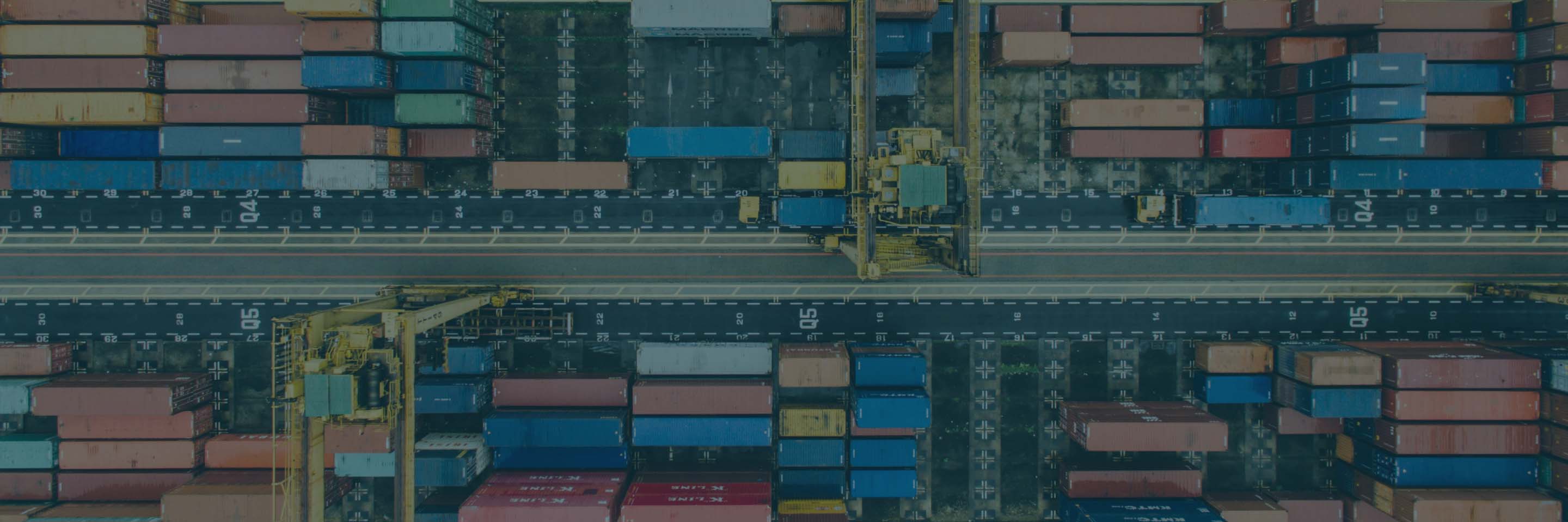
Featured Posts
Discover valuable resources to enhance your knowledge.