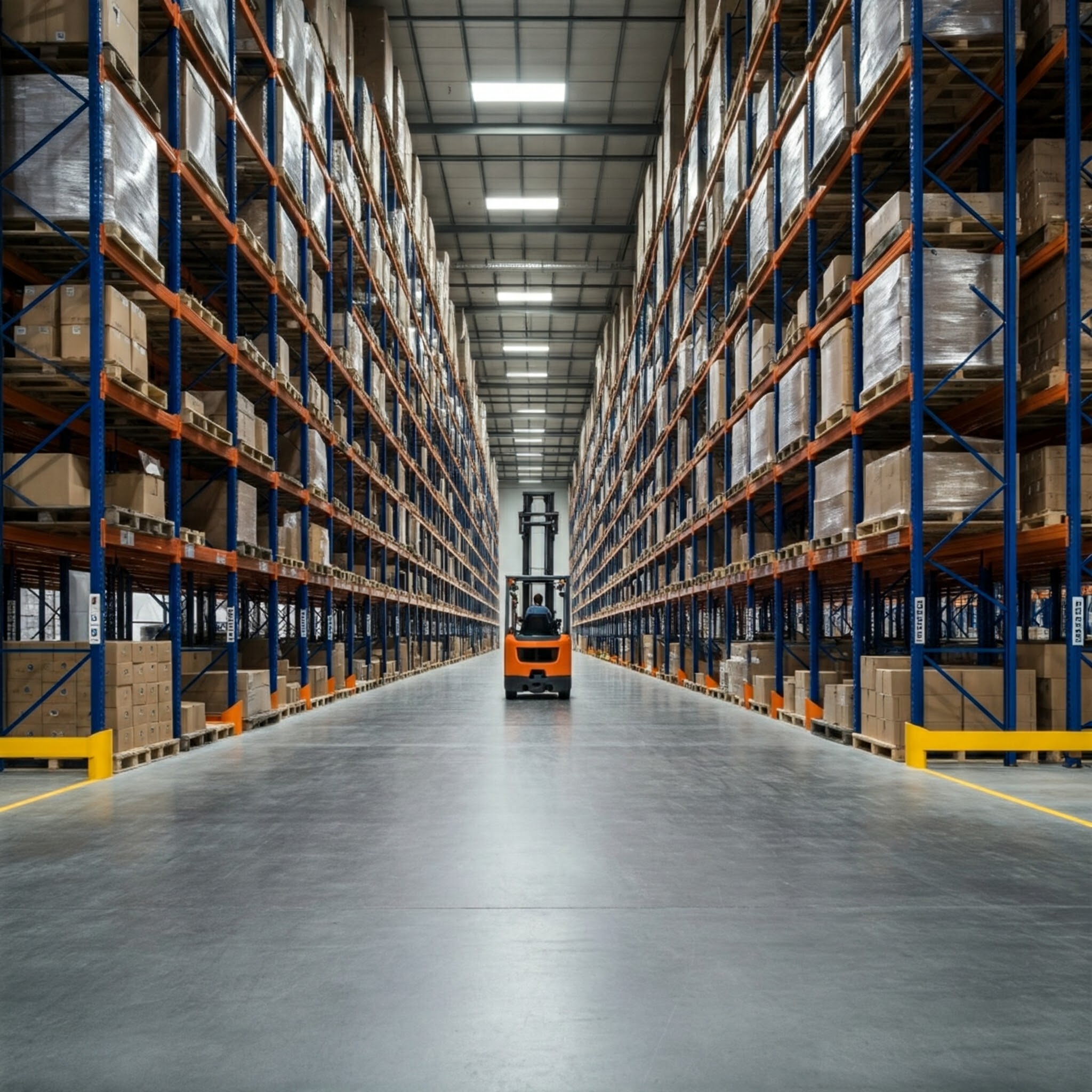
When planning a new warehouse or distribution center, optimizing storage is a critical component of the design process. It’s not just about fitting more inventory into the space—it’s about making the most of every cubic foot, reducing inefficiencies, and improving overall operational flow. A well-optimized storage system can lead to significant cost savings, faster order fulfillment, and enhanced workplace safety.
Four Effective Strategies for Warehouse Storage Optimization
1. Go Vertical with Adjustable Racking Systems
The most underutilized space in many warehouses is the area above eye level. Incorporating vertical storage solutions allows you to maximize cubic capacity without increasing your building’s footprint. Adjustable racking systems provide the flexibility to accommodate different inventory types, from pallets to small parts, making them ideal for dynamic storage needs.
Benefits:
- Increased capacity: Vertical storage takes advantage of unused overhead space, enabling you to store more inventory without expanding your facility.
- Improved flexibility: Adjustable racks can be modified to fit varying product sizes, reducing wasted space and supporting product diversity.
When going vertical, ensure you have the right material handling equipment, such as forklifts or automated storage and retrieval (AS/RS) systems, to safely access higher storage levels.
2. Add Cross-Aisles for Efficient Navigation
Travel time within a warehouse is one of the most significant factors impacting productivity. Long, uninterrupted aisles may seem efficient, but they can increase picker travel distances and slow down operations. Adding cross-aisles every 50 to 100 feet provides shortcuts, reducing the time it takes to retrieve items and improving workflow.
Benefits:
- Reduced travel distances: Shortcuts allow pickers and equipment operators to navigate the facility more efficiently.
- Improved flexibility: Cross-aisles make it easier to adapt to changes in inventory locations or traffic patterns.
- Enhanced safety: Shorter travel distances mean fewer opportunities for collisions and accidents.
When implementing cross-aisles, consider their width and placement to ensure they don’t disrupt storage capacity or create bottlenecks. Properly designed cross-aisles improve navigation while preserving storage density, making them an indispensable element in a well-designed distribution center.
3. Plan Dock Placement for Workflow Efficiency
The receiving and shipping docks are among the most active areas in a warehouse, and their placement can significantly impact efficiency. A U-shaped layout, where receiving and shipping docks are adjacent, enables shared use of resources like forklifts and conveyors while minimizing product handling.
Benefits:
- Streamlined workflow: Placing docks near each other reduces the distance inventory must travel, speeding up inbound and outbound processes.
- Shared resources: Consolidating dock operations allows for more efficient use of equipment and personnel.
In addition to dock placement, consider integrating staging areas to further support efficient dock operations. For more on maximizing space while improving workflows, check out our tips on warehouse storage and space utilization.
4. Separate Staging Areas for Inbound and Outbound Goods
Without clear separation, staging areas for inbound and outbound goods can become chaotic, leading to shipment delays and errors. Designing dedicated zones for each function ensures that inventory flows smoothly and reduces the risk of cross-contamination between shipments.
Benefits:
- Improved organization: Dedicated spaces prevent inbound goods from getting mixed with outbound shipments, making inventory management more accurate.
- Reduced errors: Clearly defined zones reduce the likelihood of picking or shipping mistakes.
For maximum efficiency, position staging areas near their respective docks. This minimizes travel distances and keeps operations flowing seamlessly.
Bringing It All Together
Optimizing storage in your warehouse or distribution center isn’t a one-size-fits-all approach. Each facility has unique needs based on its inventory, order volumes, and operational goals. However, these four strategies—utilizing vertical space, adding cross-aisles, planning dock placement, and separating staging areas—are universally effective principles that can significantly enhance your warehouse’s performance.
Additional Considerations
- Technology Integration: Tools like warehouse control systems (WCS) and inventory management software can help monitor storage usage and guide optimization efforts.
- Safety Measures: Ensure all storage designs comply with safety regulations to protect workers and inventory.
- Scalability: Design your warehouse with future growth in mind, leaving room for expansion or reconfiguration as business needs evolve.
By incorporating these strategies into your facility’s design, you’ll not only optimize storage but also improve workflow, accuracy, and employee safety.
Ready to Optimize Your Warehouse?
At Tompkins Solutions, we specialize in creating custom warehouse designs that maximize efficiency and support your business goals. With over 40 years of expertise, we help companies like yours transform their supply chain operations with innovative solutions and proven strategies.
Ready to take your warehouse to the next level? Contact us today to start the conversation.
How can we help improve your supply chain operations?
Schedule a consultation or contact Tompkins Solutions for more information.
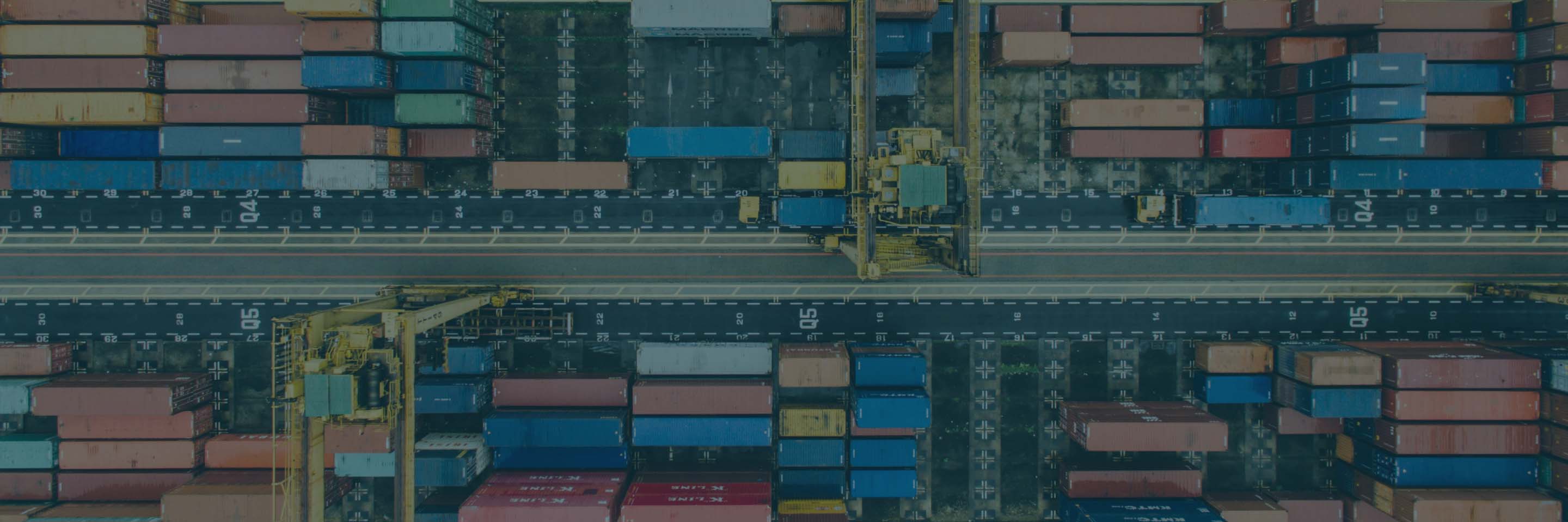
Featured Posts
Discover valuable resources to enhance your knowledge.