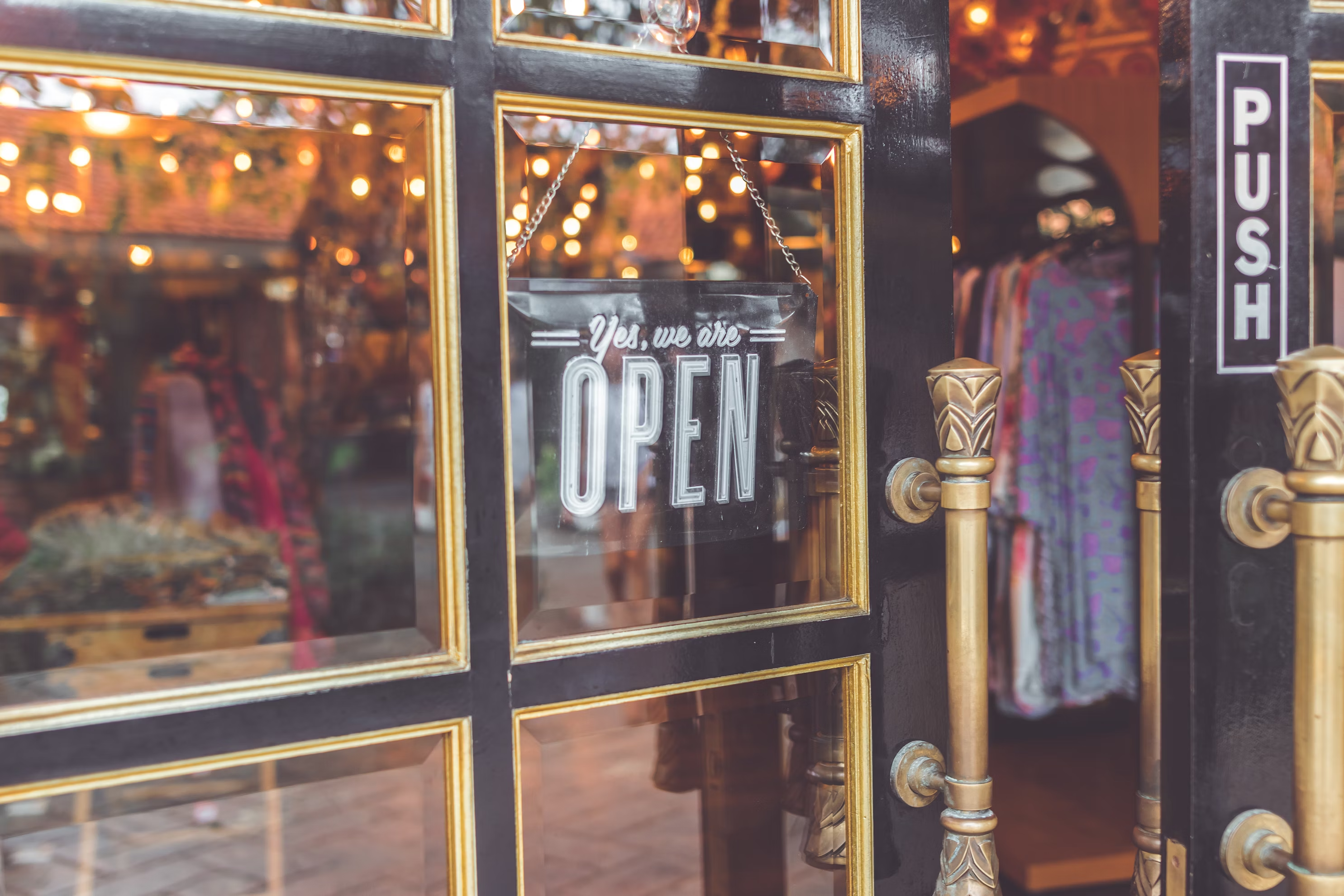
Store replenishment is a critical link in today’s retail supply chain—especially in an era where customer expectations for product availability and fast delivery are at an all-time high. Yet, if you are operating a distribution center (DC) or managing a warehouse primarily focused on bulk shipments or eCommerce fulfillment, you may not have spent as much time thinking about the nuances of replenishing physical retail stores.
In essence, store replenishment is the process of restocking retail shelves with just the right amount of inventory to meet projected demand, all while minimizing carrying costs and reducing the risk of stockouts. This article will break down the concept of store replenishment for the warehouse operator who’s already familiar with automation, but may not be as versed in the finer details of how store replenishment works—or why it matters.
What Is Store Replenishment?
At its core, store replenishment is the systematic process of transferring products from a central warehouse or distribution center to individual retail store locations. The overarching goal is to ensure that each store has the optimal amount of stock on the shelves (or in the backroom) at any given time. The process typically involves demand forecasting, inventory monitoring, and automated order generation to send the right quantities of product to each retail location.
For a warehouse operator, the difference from standard bulk order picking or eCommerce fulfillment might seem subtle at first. However, store replenishment is often driven by point-of-sale (POS) data, planogram requirements, and store-specific sales patterns. This means you’re dealing with more frequent, smaller shipments that need to align precisely with each store’s throughput. Done effectively, store replenishment can minimize inventory holding costs, reduce the risk of overstock/understock, and maintain the in-store customer experience.
In full operation, a high functioning replenishment strategy keeps your business running efficiently, and keeps stores stocked with the right levels, at the right time, all the time - helping you:
Optimize Inventory. Retailers typically operate on slim margins, so the cost of carrying excess stock can quickly erode profits. By continuously monitoring store inventory levels, you replenish only when needed and in the correct quantities.
Avoid Stockouts. Shoppers who visit a physical store expect popular items to be on the shelves. An efficient replenishment strategy keeps shelves stocked without overloading the store’s limited backroom space.
Predict Demand. From the DC perspective, precise replenishment reduces the number of emergency or ad hoc shipments. It also leads to more predictable picking schedules and truck loading. Over time, this predictability can help you plan labor and optimize your warehouse automation systems more effectively.
How a Typical Replenishment Operation Works
To effectively manage store replenishment, warehouse operators need to understand and optimize several key components that work together to create a seamless supply chain flow. Let's examine these critical elements in detail:
1. Demand Forecasting and Planning
Much of store replenishment hinges on understanding how much product will sell at each retail location over a certain time frame. Forecasting can be influenced by seasonality, promotions, local events, and consumer trends. Modern forecasting tools rely on sales history, real-time POS data, and machine learning algorithms to continually refine these projections.
2. Inventory Visibility
You can’t replenish if you don’t know the status of on-hand stock. Achieving accurate inventory visibility within both the distribution center and each store is crucial. This requires strong integration between the warehouse management system (WMS) and the retailer’s in-store systems.
3. Replenishment Triggers and Thresholds
When product levels at a store drop below a predefined threshold or reorder point, a replenishment order is triggered. The warehouse receives this order, picks the items, packages them, and arranges shipment to the store. Many retailers manage replenishment at a more granular level, factoring in shelf capacity, sales velocity, and promotional forecasts.
4. Transportation and Delivery Coordination
Store replenishment is tightly linked with last-mile logistics, albeit from DC to store rather than DC to consumer. Depending on the retailer’s network, this might include dedicated routes, multi-stop truckloads, or even cross-docking to ensure timely deliveries.
The Role of Warehouse Automation
If you’re running a modern distribution center, chances are you have some level of warehouse automation in place—from conveyor systems and automated sortation to goods-to-person (GTP) picking solutions, automated storage and retrieval systems (AS/RS), or even collaborative robots. Here’s how these technologies can directly impact store replenishment:
Order Consolidation and Sorting
Automated sorters can group items by store to expedite loading and delivery. If you have multiple stores within a truck route, sortation systems help ensure each store’s order is properly sequenced, reducing unloading chaos at the store.
Robotic Picking
Collaborative or robotic picking can speed up the selection of items that need replenishment. Robotic systems excel at repetitive tasks, reducing picking errors and labor costs. This is especially useful if each store has small, varied orders on a frequent basis.
Goods-to-Person Systems
Automating the pick face can shorten lead times and increase accuracy. In a GTP setup, items are automatically brought to a workstation where an operator (or robot) prepares store-specific shipments. This setup reduces travel time in the warehouse, making it ideal for handling numerous smaller store orders efficiently.
Real-Time Data and Integration
Advanced WMS and warehouse control systems (WCS) are critical. They need to integrate seamlessly with the retailer’s enterprise resource planning (ERP) system and inventory management tools. This ensures that when a store’s inventory hits the reorder trigger, the warehouse is immediately notified and the automation systems can prioritize that order in the queue.
Operational Best Practices
To maximize the effectiveness of your store replenishment operations, consider implementing these proven best practices that have helped leading retailers maintain optimal inventory levels while reducing operational costs:
Leverage Real-Time Data. Instant updates on sales and inventory levels enable timely replenishment, preventing overstock and understock situations. A robust, well-integrated WMS and ERP is key.
Align Replenishment with Regular Store Operations. Retail stores often have specific times when deliveries are easier to receive (e.g., off-peak hours or certain days of the week). Coordinating DC processes with store schedules can reduce disruptions and speed up shelf restocking.
Utilize Demand Segmentation. All stores are not created equal—some might have higher turnover for specific product categories or seasonal patterns. Segment your replenishment strategy so that the busiest or highest-demand stores get priority picking and shipping.
Implement Continuous Improvement. Gather performance metrics—like order cycle time, order accuracy, cost per line picked, and on-time delivery—to spot trends and identify areas for improvement.
Incorporate Reverse Logistics. Retailers frequently move unsold or seasonal items from the store back to the DC. Automation can also streamline this reverse flow, enabling stores to return products for refurbishment, markdowns, or redistribution.
Keep Your Store Replenishment Flowing
Store replenishment is more than simply shipping a few boxes to retail locations. It’s about maintaining an optimal flow of inventory that aligns with real-world demand while leveraging the sophisticated capabilities of a modern, automated warehouse environment.
At Tompkins Solutions, we help businesses design and optimize their network to ensure store replenishment processes run smoothly alongside other distribution functions. Whether you’re looking to implement a new WMS, integrate robotic picking solutions, or fine-tune your order management system, our consulting and engineering experts can guide you toward a more efficient, data-driven replenishment strategy.
In a competitive retail landscape, fine-tuning store replenishment isn’t just a way to keep shelves full; it’s a strategic advantage that can support higher sales, stronger brand loyalty, and improved operational efficiency.
Ready to take your store replenishment process to the next level?
Contact Tompkins Solutions to explore how our supply chain consulting and automation expertise can help you meet the evolving demands of modern retail.
How can we help improve your supply chain operations?
Schedule a consultation or contact Tompkins Solutions for more information.
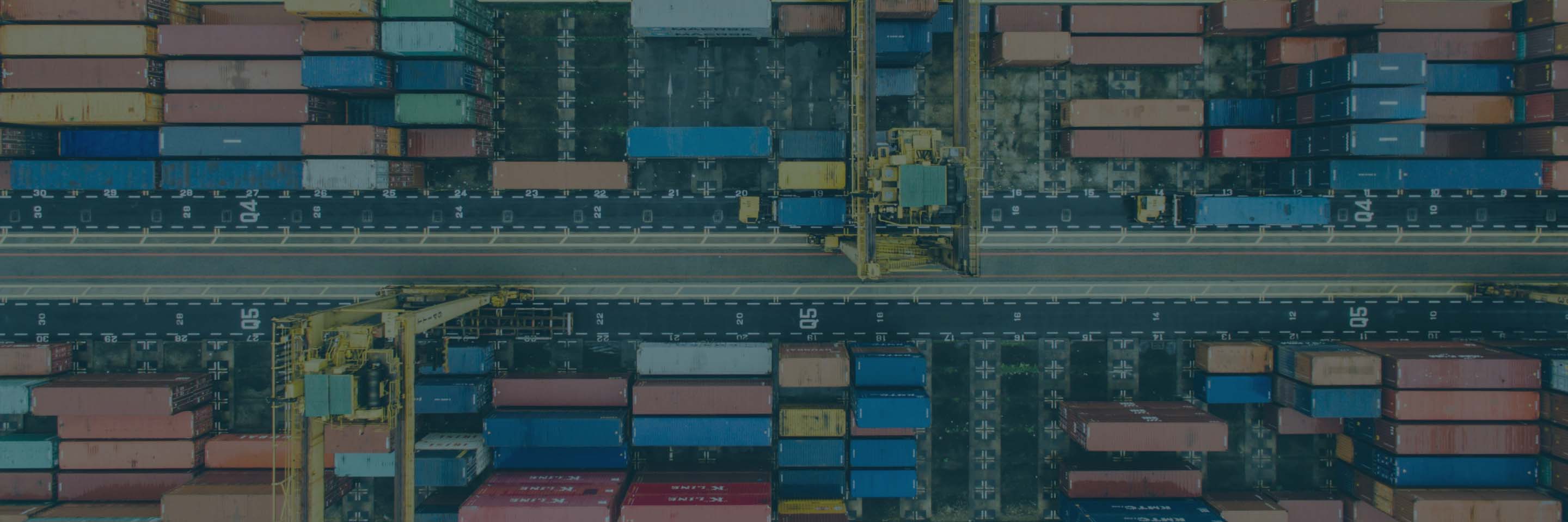
Featured Posts
Discover valuable resources to enhance your knowledge.