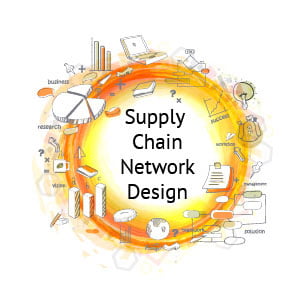
The greatest weakness of supply chain planning has been the overall topic of network design. The current state of the art network design, models a variety of networks in an attempt to define the network of facilities that allows for the satisfaction of customer service requirements at a minimal cost for transportation, inventory, investment, and operating costs.
The problems with this approach:
- An objective function of minimizing cost as opposed to maximizing profits.
- Constraining network alternatives to seller operated, 3PL operated, or a combination of seller/3PL operated and not considering a distributed logistics ecosystem.
- Customer service requirements not being consistent with future customer requirements.
- Incorrect transportation costs.
- Non-optimal inventory levels.
- Wrong investment and operating costs.
Each of these factors:
- An objective function of minimizing cost as opposed to maximizing profits: Most network designs are done to minimize cost. This is an obsolete view of the supply chain. The objective of supply chains should be to assure profitable growth. The goal should be to maximize revenue while minimize costs to maximize profitability. Most network designs ignore the impacts that improved fill rates and increased speed of delivery have on increasing revenue and thus miss the target of maximizing profitability.
- Constraining network alternatives to seller operated, 3PL operated, or a combination of seller/3PLoperated and not considering a distributed logistics ecosystem: Typical network designs look at the cost of either operating a network of owned facilities and/or of 3PL facilities, not considering MonarchFx facilities. MonarchFx facilities are neither owned or 3PL facilities. They are multi-seller, automated facilities where the seller only pays for what they use. There is no capital cost and seller operating costs are based on the MonarchFx ecosystem unit price, established based on the seller order and storage profile. The facilities are flexible with one year contracts. The MonarchFx solution can utilize the seller's existing facilities and provide additional facilities as needed over time. MonarchFx provides the seller more distribution points closer to the customer at a lower price than the seller will ever be able to do on their own- even using 3Pls. MonarchFx facilities can provide for DTC, BOPIS, wholesale, store replenishment, and many other configurations.
- Customer service requirements not being consistent with future customer requirements: Network designs typically plan for a five year planning horizon and require the prediction of the volume by geography, fill rates, and order delivery times demanded by customers. The target is to develop a definition of orders over the planning horizon, typically five years. Obtaining projections for the year ahead is difficult and trying to obtain these numbers for a five year planning horizon is a wild guess. The same challenge exists with the desired customer service levels. Do the customers want two day delivery across the U.S. or do the requirements vary by the size of city they live in? Are northeast delivery requirements the same as southeast? Is it two day now, next day next year, and same day two years from now expected? Do all customers have the same requirements? No, although most network designs treat all customers the same. What is needed is a network, such as MonarchFx, that is flexible and modular enough to change on a yearly basis and still keep capital and operating costs in check.
- Incorrect transportation costs: The most significant network modeling costs are transportation costs. Transportation costs include inbound, outbound, and trans-shipments. For inbound transportation costs, it is usually assumed that all sourcing stays the same for the five year planning horizon. For outbound, how do you handle the different requirements of two day, next day, and same day and how to handle the evolution of BOPIS and DTC? For trans-shipment what assumptions can you make here? For facility or store transfers, which of course should be minimized. Lastly, how do you establish future transportation rates and assessorial charges especially given the fast evolution of final mile delivery options? Clearly there is no way to do any of this well.
- Non-optimal inventory levels: The square-root law for the growth of distributed inventory safety stock as opposed to centralized inventory is well known and mathematically correct when stock is deployed by pushing inventory to locations. However, when deploying a demand-driven replenishment model the square-root law is not applicable. Most network design exercises use the square-root law and thus "optimize" solutions by having too few stocking points.
- Wrong investment and operating costs: Not nearly as important as transportation costs and inventory levels but still a major factor impacting the "optimal" network design, the accuracy of the investment and operating costs going forward. It is not possible to accurately predict these costs over a five year horizon so when these costs are added to tremendous amount of uncertainty in the above four factors and the rapidly changing material handling technology used to fulfill orders, we find that huge mistakes are often made. There is a tremendous amount of shifting in networks over time and a tremendous amount of money wasted.
After working on network planning for the last 40 years (yes we began network modeling in 1978 on a Radio Shack TRS-80 computer) and understanding the huge level of disruptions and change occurring in today's business environment, I am firmly of the opinion that what was once a great planning tool, network design, has become woefully obsolete given today's dynamic environment and the existence of solutions like MonarchFx.
How can we help improve your supply chain operations?
Schedule a consultation or contact Tompkins Solutions for more information.
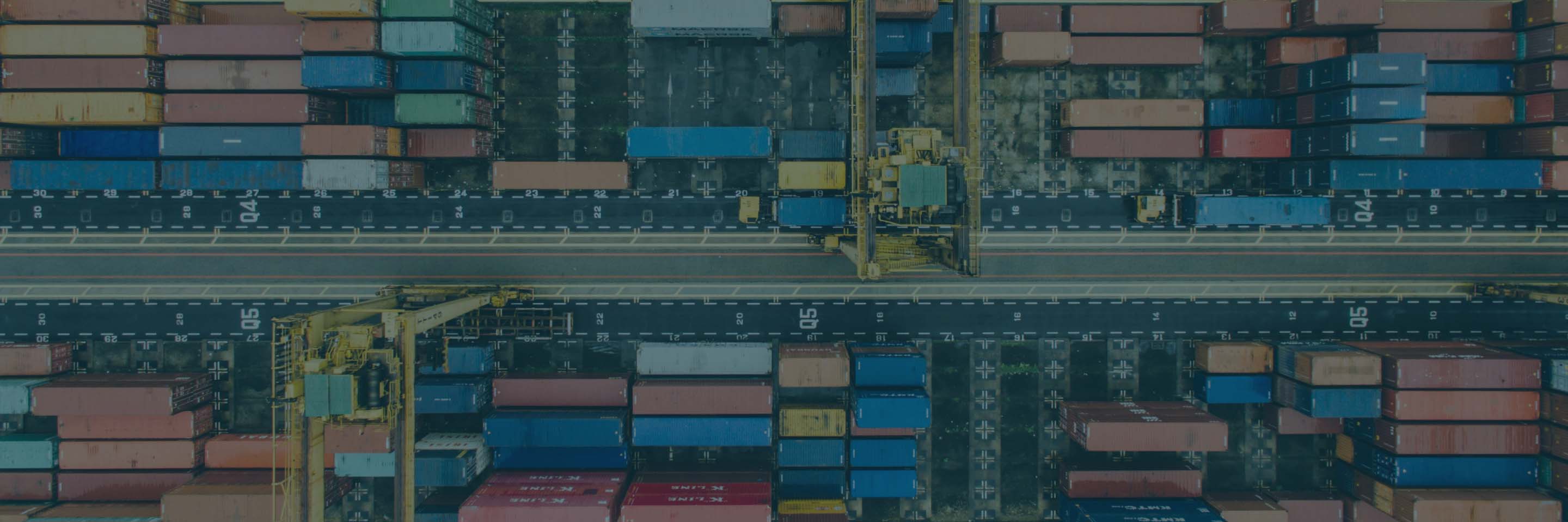
Featured Posts
Discover valuable resources to enhance your knowledge.