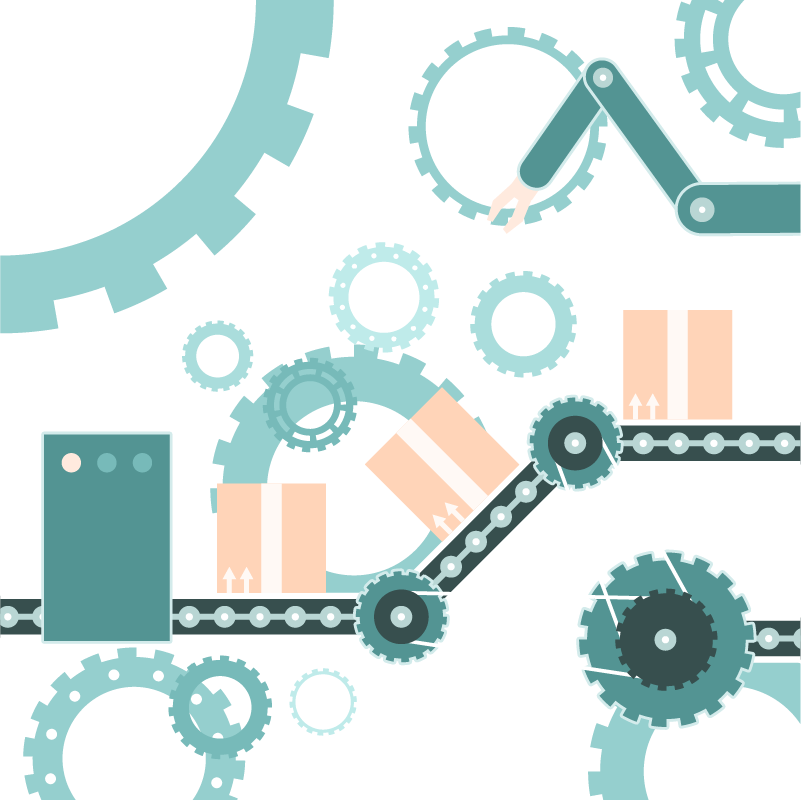
What is the state of automation advancements in the warehouse and their viability?
Advanced automation in the warehouse has been the area with the largest growth over the last five years. There has been a major shift in thinking in recent years as it relates to higher levels of automation in warehousing. Gone are the days where fully automated solutions were quickly written off due to their high price tags or fear of the technology. Several factors play in to this new mode of thinking.
First is the labor pool. Recently, it has become increasingly difficult to find good employees. This is partly due to the aging of the baby boomers and less available resources in the younger workforce. There is also growing competition from increased presence in prime warehousing areas all fighting over the same labor pool. Couple this with the rise in wages and benefits and it makes higher automation options more attractive.
The cost and options available with highly automated systems have also had a big impact on decision makers. Increased competition among vendors, shift of manufacturing of certain equipment to the US, and newer, more scalable options have all made automation more viable. Gone are the days where the only highly automated options were AS/RS, AGV, carousel, and unit sorter systems. Today product offerings are growing in the areas of automated goods-to-man stations, autonomous pick carts, picking robots, automated put systems, unit sortation robotics, and the list is growing every day. When looking at improving your facility's productivity and utilization, serious consideration should be given to these up and coming technologies as the paybacks may be quicker than you think.
What are some of the recent changes in thinking when it comes to warehousing planning and/or design?
The only certainty you can count on in today's logistics world is that there is going to be change. Today's logistics and supply chain leaders are faced with a constantly changing landscape. Changes in business model, marketplace, customers and their demands, competitors, etc., are all being dealt with on a yearly, monthly, and even weekly basis.
Gone are the days of the 10-year or even five-year roadmaps. Executives are now focusing on the next 18 - 36 months and any adjustments needed to meet the demands on the immediate horizon. Odds are whatever you are doing today will be different in a few years. The key to any logistics network is the ability to be nimble and adjust to the changing demands.
A good measure of a facility design is the flexibility the proposed solution offers to the end user. The key is to not only be flexible with the physical layout and allow for growth/modifications, but also the flexibility of the actual equipment. Can it handle higher volumes? Can it be expanded or modified? Will it handle a different product mix? Can it be relocated easily? These and other questions should be asked at each step of the design process to ensure that you are setting yourself up to not only be successful in the short-term but allows for the greatest ability to morph into what your facility needs are in the future.
How can warehouses become Unichannel friendly?
Our concept of Unichannel is a new approach to a business's online and in-store customer base. The main premise is that a customer is a customer, regardless of how or where they order. For a company to gain and retain customers it must meet the myriad of ways customers want to buy your product online delivered at home, in store on shelf, online to be picked up at store, and the list goes on and on.
The most effective way to fulfill these orders, as well as store replenishment shipments, would be in a single site. If each process were built as a separate stand-alone functional area the size and cost of the facility would sky rocket, not to mention the compartmentalization and inefficiencies you would build into your warehouse.
What if all these "channels" could share a common inventory, common pick location, and all flow to a single sorter, all comingled with one type of order undistinguishable from other types? This is where automation can help. With today's unit sorters and robotics solutions this "what if" is now a reality. Companies can get the biggest bang for their buck by leveraging this high-powered system to process all types of orders. This allows operations to be able to better handle the peaks and valleys in their different segments and help keep the overall building volumes level loaded. By taking such a flexible approach a company is also better suited to meet their customer's future demands as well. With a well implemented solution the sky really is the limit for your facility.
Stop by our Modex 2018 booth #B727 April 9th through 12th in Atlanta, GA. Come any day to learn about the latest technology available to enhance, build, and complete an advanced, smart, and efficient supply chain.
How can we help improve your supply chain operations?
Schedule a consultation or contact Tompkins Solutions for more information.
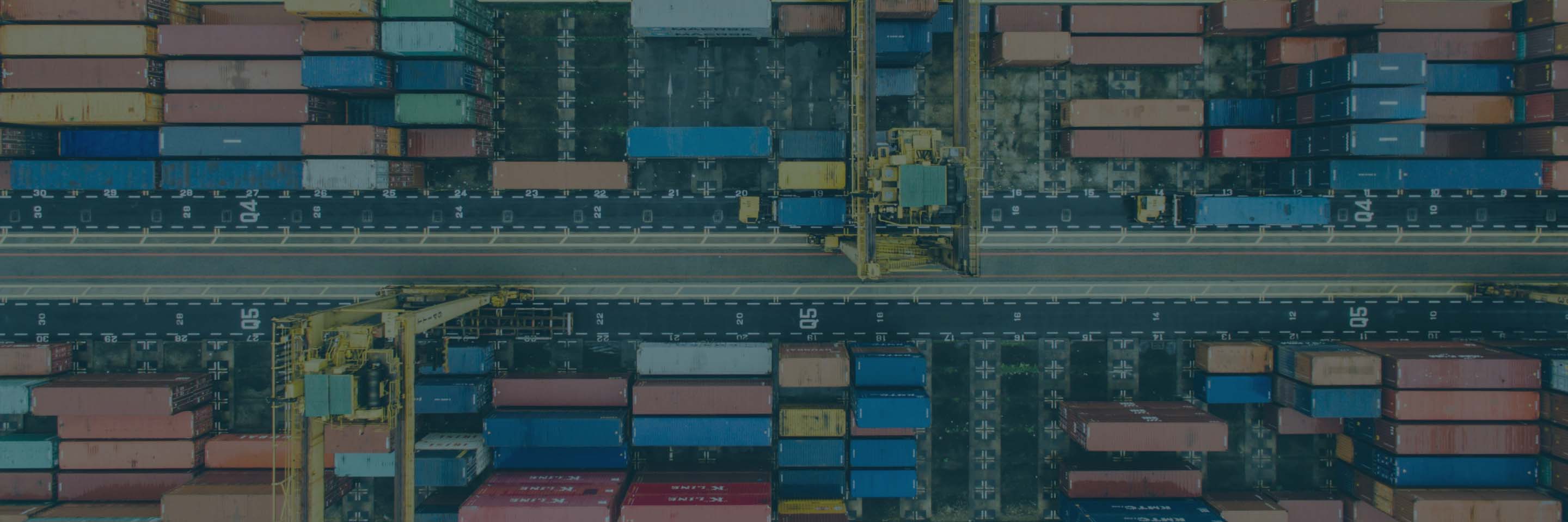
Featured Posts
Discover valuable resources to enhance your knowledge.