Warehouse Automation: How to Select the Best Solution for Your Distribution and Fulfillment Operations
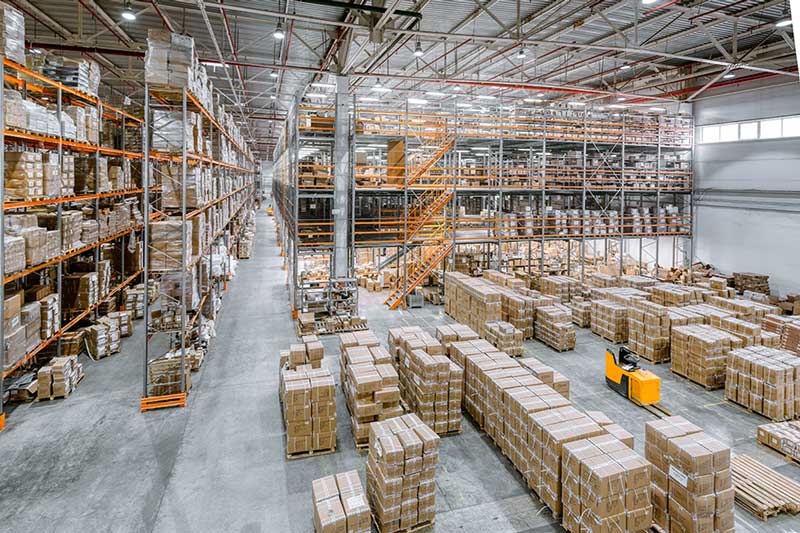
A common question we receive from clients today is when does it make sense to automate warehouse operations. Automated material handling equipment and robotic solutions are becoming a top priority for many supply chain professionals struggling to overcome disruptions and keep up with the demands of changing industry trends.
According to eMarketer, online retail sales in the U.S. are projected to reach $933 billion this year and are on track to top $1 trillion in 2022. The increase in e-commerce sales has impacted many areas of order fulfillment, including major shifts in order profile and volumes. Distribution operations that were originally designed to process pallets of items for store replenishment are now having to handle thousands of orders of a handful of items for individual customers.
These changes in order profile and volume have also led to increased space and labor requirements. According to research by Prologis, e-commerce fulfillment requires three times the labor and space of traditional logistics operations.
With the current warehouse space and labor shortages, many companies are turning to automation to help fill growing order volumes and meet carrier cutoff times. While automation can streamline many processes and increase speed and efficiency, the best solution will depend on your unique requirements, goals and objectives. Here are a few things to consider when evaluating automation for your distribution and fulfillment operations:
Warehouse Space and Layout
Warehouse space is at a premium, making it essential to understand how automation fits within your current layout. Automated storage and retrieval systems (ASRS), for example, utilize vertical storage and operate in narrow aisles, freeing up valuable floor space. Explore how ASRS and similar technologies can transform your layout in 5 Ways Warehouse Automation Optimizes Dock Operations.
Volume
One of the most important metrics in determining if automation is right for your operations is volume. Define your planning horizon, sales forecasts and other key business metrics that may impact future volumes and requirements. Since peak volumes can be up to 20 times more than average throughput, it's also important to understand the seasonality impacts of your business and select a solution with the flexibility to adapt and scale to meet changing demands.
SKU and Order Profiles
In addition to volume, SKU and order profiles also play a large role in determining the best type of automation for your operations. Gather data on SKU size (dimensions and weight), velocity (fast movers vs. slow movers) and flow, as well as the number of SKUs and items per order. Distribution centers that process orders for store replenishment will require much different material handling systems than fulfillment centers that ship e-commerce orders directly to consumers. Learn how to align SKU profiles with automation in Warehouse Automation: Are AMRs the Right Solution for Your Logistics Operations?.
Costs
One of the biggest myths surrounding warehouse automation is that it's too expensive. The reality is, while automation requires a significant upfront investment, it's still a more affordable option for many high-volume operations due to the limited availability and increasing cost of labor today. According to the Bureau of Labor Statistics, the average hourly rate for warehouse workers reached a record high $23.08 in July, and there were 490,000 unfilled jobs in the transportation and warehousing sector-a more than 65% increase over the previous year. When calculating the true value and ROI of automation versus labor, look beyond direct costs and consider additional savings and efficiencies gained such as increased efficiency, productivity, order accuracy and employee retention.
Lead Times
Steel and labor shortages are causing massive manufacturing delays across the industry, with lead times currently four to six months or longer for most material handling equipment. While the average installation and training time will vary widely based on the specific solution, it's important to start planning as early as possible to ensure your operations can keep up with growing demands. For guidance on implementing automation systems within these constraints, review Warehouse Automation: How to Select the Best Solution for Your Distribution and Fulfillment Operations.
With the increase in order volumes and demand for warehouse space and labor, the question is no longerif you need to automate but when you need to automate. When volume and velocity exceed the available floor space and labor, automation becomes the only way to meet growing demands. Combining different types of robots and automated material handling systems into your warehouse design can help optimize fulfillment operations and set your business up for future success.
Determining the right level and type of automation for your operations can be challenging. With decades of experience in material handling integration and equipment, Tompkins Solutions' experts can help you select the best solution for your unique current and future needs.
Ready to take the next step? Learn more about automation trends and strategies in 10 Trends in Warehouse Automation.
Contact us today to start planning your warehouse automation project.
How can we help improve your supply chain operations?
Schedule a consultation or contact Tompkins Solutions for more information.
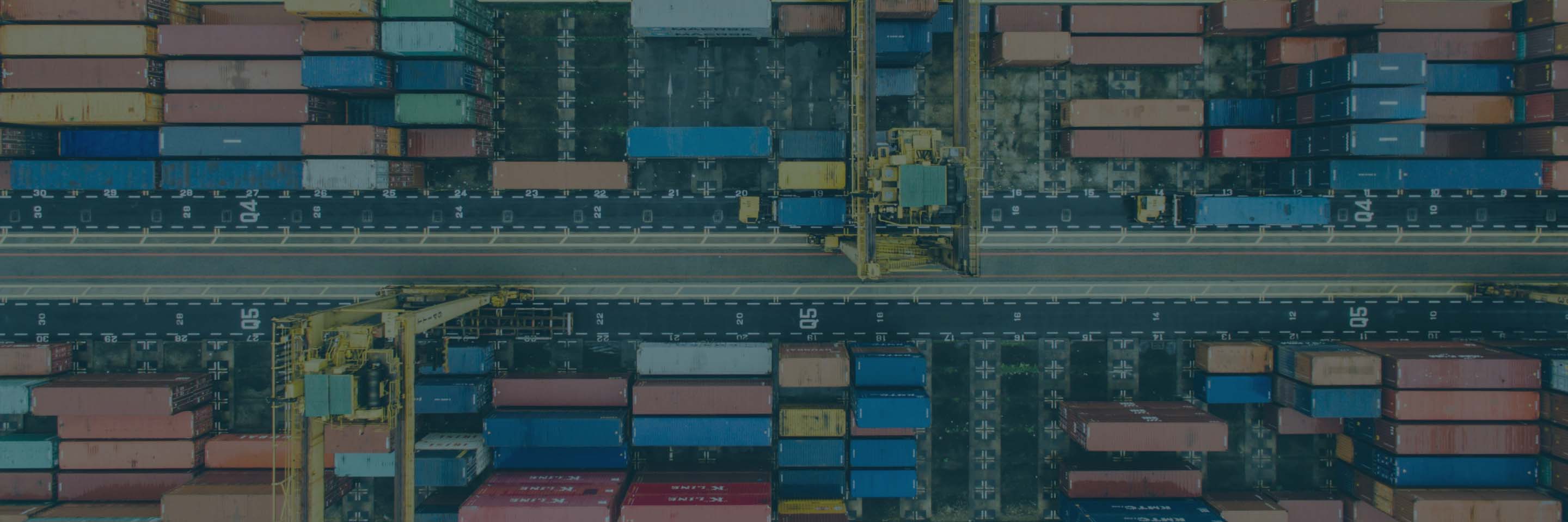
Featured Posts
Discover valuable resources to enhance your knowledge.