While the core principles outlined in this blog remain essential for designing a successful distribution center, the logistics landscape has continued to evolve since its original publication in August 2022. Today, the emphasis on flexibility and scalability in warehouse design is more critical than ever, driven by increased demand for faster fulfillment and the integration of advanced technologies like AI-driven warehouse control systems (WCS) and robotics. Additionally, challenges such as labor shortages and sustainability goals have heightened the importance of automation and energy-efficient design features.
This guide provides a timeless framework, and its relevance endures as businesses navigate an increasingly dynamic supply chain environment. By incorporating updated considerations—like modular layouts and adaptive sortation systems—companies can future-proof their operations while addressing current and emerging challenges.
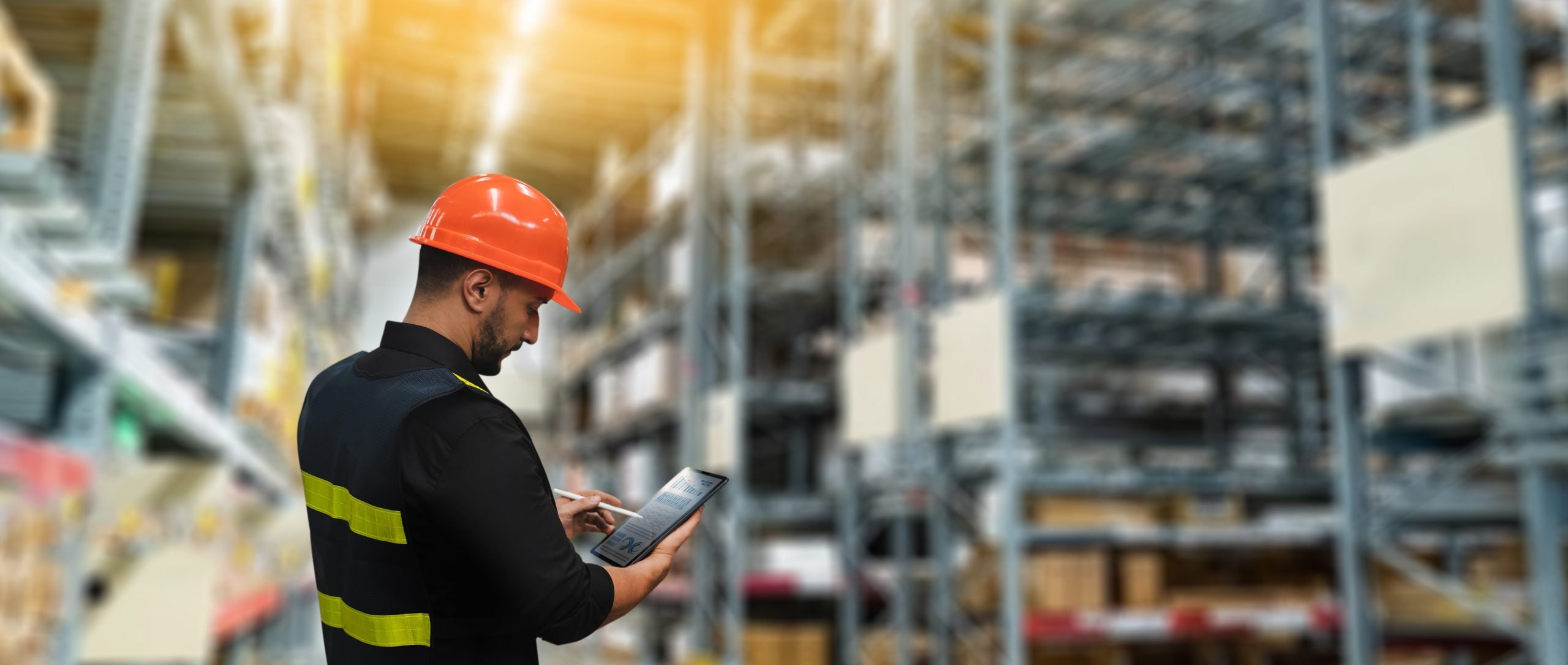
Designing a new distribution center can be a difficult task. Whether it is your first or 100th time, greenfield or brownfield project, there are several key areas to focus on when designing a new facility. Below are the seven essential steps to take to ensure a successful warehouse design project, from site selection all the way to go-live.
1. Network Study
Prior to beginning any facility design project, companies must first determine the best location for the new warehouse. Performing a network study will help you determine the optimal place to locate your next facility within your overall network design.
If you're wondering whether your current warehouse design is still meeting operational demands, check out our guide on How to Tell When It’s Time to Update Your Warehouse Design.
2. Establish Building Parameters
The next step is to define the specific requirements of the new warehouse. Questions to answer during this stage include:
- What is the intended use of the warehouse (cross-dock, transload, e-commerce, distribution, omnichannel fulfillment)?
- When does the warehouse need to be fully operational?
- What are the requirements for throughput and storage capacity? This may become more apparent during the conceptual design phase.
- Are there any financial limitations?
3. Data Development & Analysis
Once you have identified the optimal location and building requirements for your new distribution center, it is time to collect operational and historical data. This should include details about material flow and volumes, item master with product families, sizes, handling characteristics, order profiles and frequency. The following data should also be gathered during this step:
- Transportation information for inbound and outbound shipments
- Current inventory levels, stocking policies and requirements
- Truck volumes and movements on site
- Customer service requirements
- Define the basic warehouse essentials and subsidiary operations: picking, packing, VAS, returns, quality control, forklift charging, breakrooms, bathrooms, lockers, facility maintenance & cleaning, trucker lounge, etc.
- Develop a growth plan with future requirements and throughputs for storage, picking, packing, fulfillment and shipping profiles
- Collect cost data: building rent, labor, utilities (water, trash, gas & electricity), material handling equipment costs (including associated maintenance), building maintenance and security
Additionally, don’t forget to evaluate how well your warehouse storage and space utilization align with your growth plans. Learn more about this in our blog, Warehouse Design: How to Improve Your Warehouse Storage and Space Utilization.
4. Define the Warehouse Operations
With all of the appropriate data in hand, it is now time to define the warehouse operations. Your description should include the different functions (receiving, putaway, replenishment, order picking, value added services, packing, shipping, returns, quality control, inventory cycle counting, cross-docking, transloading, sortation, etc.), as well as how often these tasks are happening (single shift, two shifts or three shifts).
Once you have a complete description of the warehouse operations, you will need to develop a material flow diagram with a walk-through from the moment the material enters the building to the moment it leaves the building. This diagram will help your warehouse design consultant develop the perfect warehouse layout tailored to your unique needs.
5. Conceptual Design
Now that you have fully defined the operations, it is time to work with your warehouse design partner to develop a conceptual design to identify and establish critical building characteristics, including the number of dock doors, square footage, clear height, etc. This will prepare you to confidently select the proper site for your new warehouse.
A good warehouse consultant should provide a baseline design and an alternate design. During this time, your warehouse design partner will develop rough order of magnitude (ROM) pricing for budgetary purposes. In addition to ROM pricing, they should estimate equipment lead times and create a high-level roadmap to go-live.
During the conceptual design phase, you will also work with your warehouse consultant on the following areas to help determine the right building for your operations:
- Evaluate material handling equipment options
- Draft high-level procedures and information system requirements
- Evaluate design flexibility
- Estimate equipment quantities
- Estimate staffing levels
- Estimate CapEx and operations costs
- Assess the conceptual design against the requirements of your business
Your consultant should also provide a high-level roadmap and alternative designs for comparison. To understand the benefits of working with experts, visit 5 Reasons to Select a Full-Service Supply Chain Consulting Firm for Your Warehouse Design Project.
6. Site Selection Process
Once you have established the parameters for a new facility, you can use this information to determine whether new construction or an existing building will be the best fit for your operations. Below is some information on the different options that may be available:
New Construction
If proceeding with new construction, you will need to decide between a build-to-suit or spec building. Build-to-suit is when you enter into an agreement with a developer for a custom building tailored to your specific needs. Depending on the market, a spec building is already built or in the process of being built with a cookie-cutter design that appeals to a large market of warehouse clients.
The benefit of a build-to-suit is that you have the opportunity to upgrade certain items prior to completion of the build. For example, you can upgrade the lighting, dock packages, windows, building climate control, yard size, concrete vs. asphalt yard, landscaping, options for other amenities such as warehouse breakrooms, bathrooms, trucker lounge, etc. In some situations, you can even define the specifications of the concrete thickness and opt for reinforced roofing to hang conveyor equipment. The downside of a build-to-suit is that you are starting from the beginning of the design, which will extend your timeline to go-live.
While a spec building can be completed in a shorter timeframe and at a lower cost than a build-to-suit, it is built to code with the minimum requirements and offers limited customization.
Existing Buildings
It is critical to perform some preliminary due diligence when acquiring an existing building. Oftentimes older buildings were built to a previous version of building code. This means that the building may not meet current standards by the local authority. Some common issues that may arise are the concrete slab details, fire suppression system and the Americans with Disabilities Act (ADA) requirements.
Concrete slabs in older buildings may not be as thick as slabs in newer buildings. This doesn’t mean that you need to pour a new slab, but it does mean that the structural engineer may not allow as much weight to be stored on the racks or may limit the overall height of the racking. Therefore, it is critical to have accurate data for the material being stored in the building prior to selecting a facility.
Not all fire suppression systems are the same. There are many factors that determine what system the builder puts into the building. Some of the common types are ESFR (Early Suppression, Fast Response) and design density systems. It is important to know your material commodity classes prior to selecting a building. If the commodity class and existing fire suppression system are incompatible, it may require a sprinkler modification to pass fire inspections.
In areas such as Los Angeles, it is common to find older buildings that were built before the ADA requirements were put in place. Therefore, you many need to add ramps and other accessibility features to the building in order to comply with the current standards.
Dimensional data plays a crucial role in site selection and layout planning. Learn more about its importance in The Importance of Dimensional Data in Warehouse Design.
7. Finalize a Detailed Design
Now that you have selected a building, it is time to send the CAD file to your warehouse consultant to drop in the conceptual design and work through any revisions required to make it the perfect fit. Once the final design is completed, your warehouse design partner will begin the process of creating a firm and actionable proposal.
Since distribution operations are not “one size fits all,” designing a new warehouse requires strategic planning and analysis to ensure long-term success. An experienced supply chain consultant can work with your company to conduct a network study and develop a customized warehouse design capable of supporting your unique operations and current and future business requirements.
Contact us today to learn how we can help you determine the optimal design for your new warehouse.
How can we help improve your supply chain operations?
Schedule a consultation or contact Tompkins Solutions for more information.
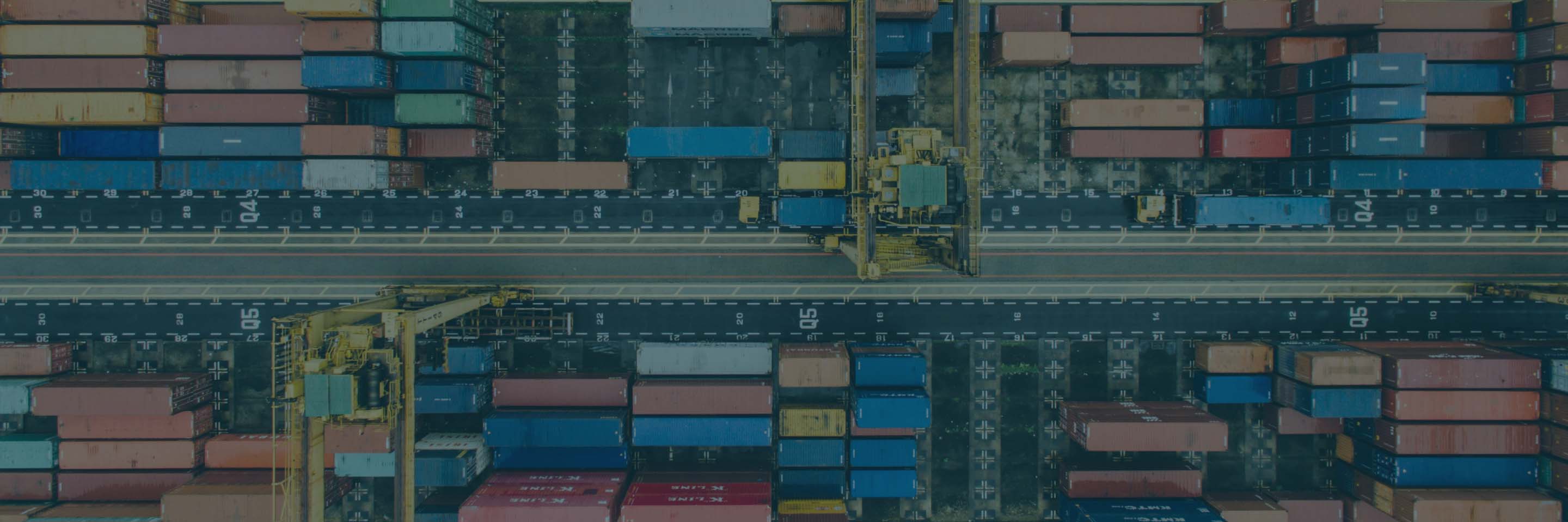
Featured Posts
Discover valuable resources to enhance your knowledge.