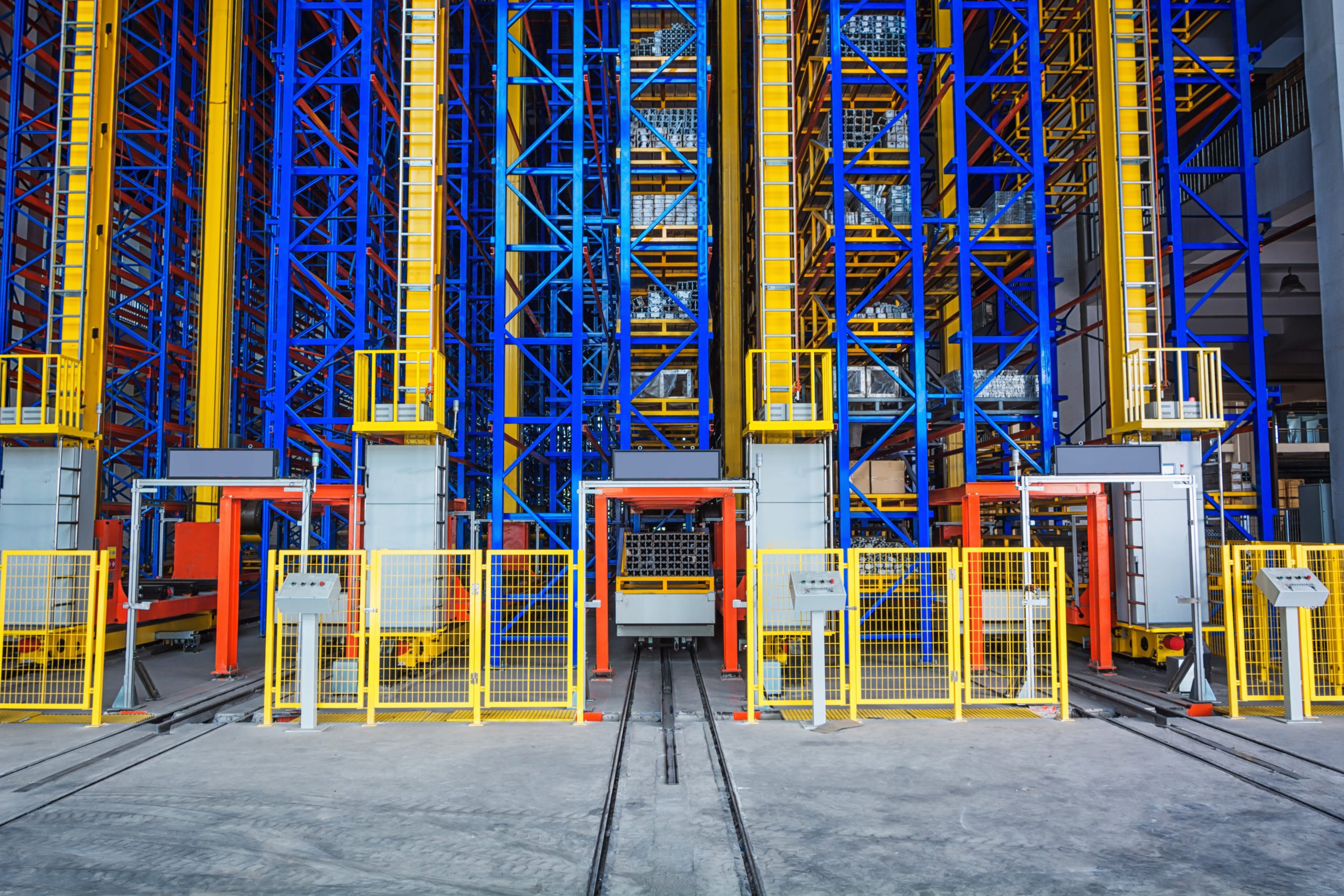
There were nearly 8,000 supply chain disruptions in the first half of 2022—a 46% increase over the first half of 2021—according to Resilinc. As a result, retailers are increasing inventory to minimize the risk of shortages and keep up with growing customer demands and e-commerce sales. With warehouse space and labor extremely limited and expensive, it’s important to have the right warehouse storage solutions to increase efficiency and maximize space utilization.
Characteristics of an Ideal Storage Solution
The best warehouse storage solutions are dense, dynamic, and flexible, providing high utilization throughout the year. Selecting the appropriate storage medium depends on several factors, including your warehouse design, SKU counts, inventory levels, and order profiles. Optimizing your warehouse layout to align with these factors is essential for operational success. For insights into recognizing inefficiencies, explore How to Tell When It’s Time to Update Your Warehouse Design.
The right storage mediums will vary depending on your unique requirements and distribution operations, including your warehouse design, inventory and SKU counts, and order volumes and profiles. The ideal warehouse storage solution is dense, dynamic and flexible, and provides high utilization throughout the year.
Overview of Storage Systems
There are many different types of warehouse storage systems, from manual to semi-automated to fully automated. Each solution has a minimum SKU-to-pallet ratio in order to achieve high utilization. Below is an overview of some of the top warehouse storage solutions for distribution operations.
Selective Pallet Rack
Selective pallet racking is a “first in, first out” (FIFO) single-deep storage solution that provides 100% selectivity of the pallets stored in the rack system. This low-cost solution is ideal for a warehouse with a wide array of low-volume SKUs.
Double-Deep Pallet Rack
Double-deep pallet racking is a “last in, first out” (LIFO) 2-deep storage solution that provides 50% selectivity of the pallets stored in the rack system. This solution increases storage density by providing the twice the amount of pallet storage in half the amount of space.
Push Back Rack
Push back rack is a LIFO solution that can store anywhere from two to six pallets deep. This versatile solution offers a higher storage density than other racking systems and is best used in warehouses with a high pallet count of the same SKU.
Pallet Flow Rack
Similar to push back rack, pallet flow racking systems offer a higher storage density (anywhere from two to 20 pallets deep), but are FIFO, making them an ideal solution for time-sensitive or perishable goods.
Drive-In Pallet Rack
Drive-in pallet racking is a LIFO solution that can store an unlimited depth of pallets. With maximum storage density and low selectivity, these systems are ideal for storing large quantities of homogeneous products or items that are not time-sensitive.
Bulk Storage
Also referred to as “floor stacking,” bulk storage can support both FIFO and LIFO and requires no physical equipment, with products stored directly on the floor several pallets deep. Bulk storage offers the highest storage density with the lowest level of selectivity, so it is only desirable if you have small number of SKUs and a large volume of stackable pallets of the same SKU. While this storage solution is infinitely dense, it is governed by local fire authority for high piled bulk storage and required paths of egress.
Pallet Shuttle System
The pallet shuttle is a semi-automated high-density storage solution that can operate in both FIFO and LIFO modes. The pallet shuttle system does not have any constraints with regards to depth of pallets. The only governing factor on depth of the storage system is the quantity of pallets per SKU. This data will provide the ideal depth in order to achieve maximum utilization of the system.
Four-Way Shuttle System
The four-way shuttle is a high-density automated storage and retrieval system (ASRS) that is ideal for warehouses looking to maximize their storage capacity and automate their distribution operations. This solution includes a sophisticated software program that communicates with your warehouse management system (WMS) to automatically pick and put away pallets in the storage system. Additionally, the software can track historical and other inventory data to identify the optimal storage location for pallets to increase efficiency and throughput.
Critical Data for Optimizing Storage
Before implementing a storage solution, your warehouse consultant will need key data points to determine the best fit for your operations. This includes:
- An item master with SKU dimensions and weight.
- A 12-month inventory report to identify peaks and valleys.
- An inventory growth plan to ensure the system meets current and future needs.
Accurate data helps consultants tailor storage solutions to maximize efficiency and throughput while optimizing the use of space. Discover how data plays a crucial role in warehouse optimization in The Importance of Dimensional Data in Warehouse Design.
Preparing for the Future
Selecting the right storage system is an essential part of warehouse design, but it is just one piece of the puzzle. A comprehensive approach to layout, inventory flow, and automation ensures long-term success.
For a complete guide to warehouse design, explore Warehouse Design: 7 Essential Steps for Designing a New Distribution Center. Contact us today to learn how we can help you improve your warehouse storage and space utilization to meet your operational goals.
How can we help improve your supply chain operations?
Schedule a consultation or contact Tompkins Solutions for more information.
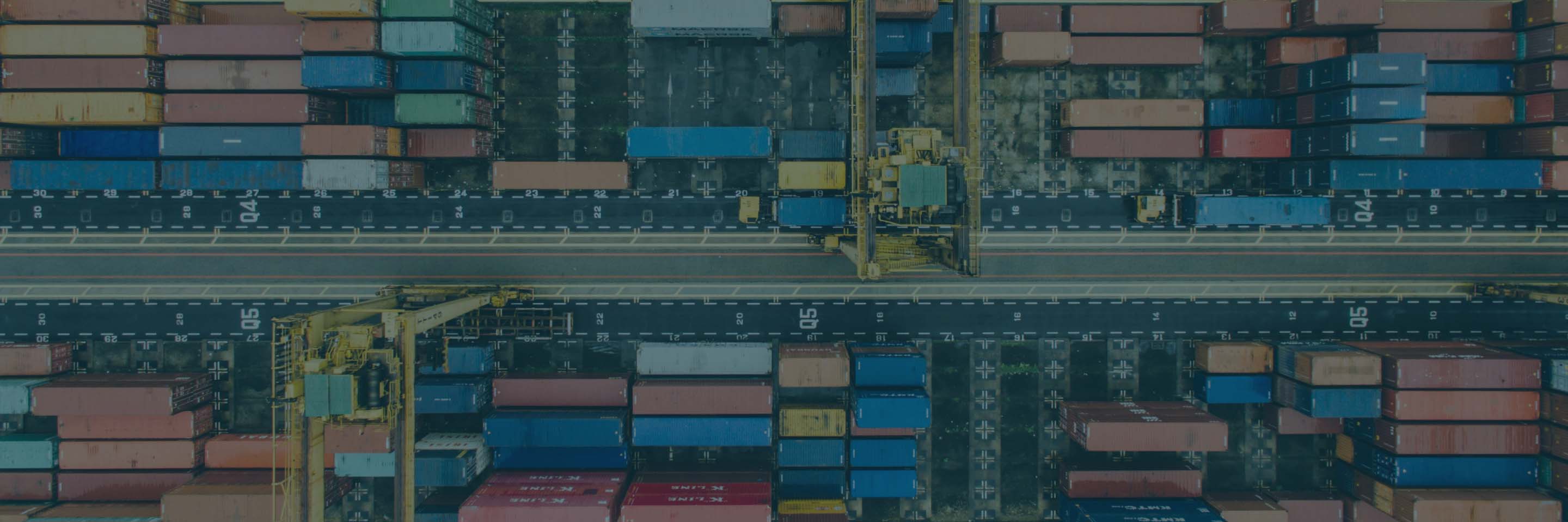
Featured Posts
Discover valuable resources to enhance your knowledge.