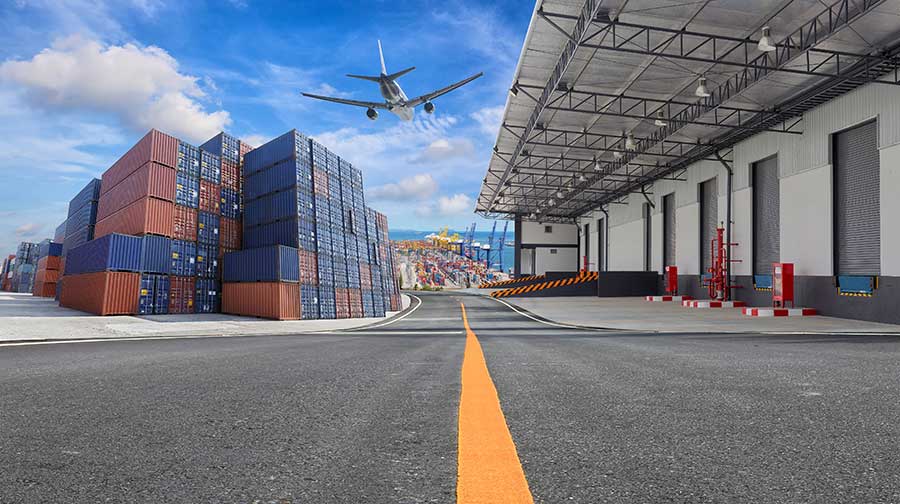
Cross-docking is a logistics strategy that involves the direct transfer of products from inbound to outbound transportation with minimal or no storage time. This approach can significantly enhance supply chain efficiency by reducing handling times and storage costs. However, implementing cross-docking presents challenges that can be mitigated through thoughtful warehouse design.
Key Challenges with Cross-Docking
1. Coordination Complexity
Effective cross-docking requires precise synchronization between inbound and outbound shipments, demanding close coordination among suppliers, manufacturers, and retailers. Real-time visibility into inventory levels is essential to prevent delays and bottlenecks.
2. Operational Requirements
The process depends on the availability of sufficient transport carriers and reliable suppliers to ensure timely deliveries. Additionally, cross-docking is labor-intensive, necessitating adequate staffing to manage the swift movement of goods. Implementing cross-docking also requires advanced technology systems for real-time tracking and communication, as well as comprehensive employee training programs to ensure operational efficiency and safety. Moreover, maintaining flexibility to adapt to demand fluctuations and unforeseen disruptions is crucial for sustaining seamless operations.
3. Infrastructure Demands
Establishing a cross-docking facility involves significant initial investment in specialized equipment and technology. Precise scheduling is crucial to maintain the seamless flow of goods through the facility.
Distribution Facility Design Considerations
1. Layout Considerations
The physical layout of a cross-docking facility significantly influences its efficiency. Smaller facilities may benefit from I-shaped or narrow rectangular designs, while larger operations might utilize L-shaped, rectangular, or T-shaped configurations. Strategic placement of dock doors, such as positioning them at 90 degrees to each other, can minimize congestion and enhance the flow of goods.
- Pro Tip: Implement advanced dock scheduling systems to precisely coordinate the arrival and departure of shipments, minimizing wait times and preventing congestion at dock doors.
2. Staging Area Design
Implementing efficient staging zones for temporary holding is vital. Dedicated areas for different product types ensure organized sorting and consolidation, facilitating quicker transfers from inbound to outbound shipments.
3. Technology Integration
Incorporating technologies like barcode scanning, RFID systems, and warehouse management systems (WMS) can automate processes and provide real-time inventory tracking. Utilizing Electronic Data Interchange (EDI) enables seamless communication between all parties involved, enhancing coordination.
- Pro Tip: Leverage real-time data analytics to monitor and optimize cross-docking operations continuously, enabling proactive decision-making and rapid response to any issues that may arise.
4. Flow Optimization
Designing the facility to minimize handling and processing times is crucial. Standardizing inbound and outbound processes and maintaining clear separation between receiving and shipping areas can streamline operations and reduce errors.
Contingency Planning & Risk Management
Developing alternative transportation routes and maintaining backup plans for unexpected events are essential to ensure continuity. Establishing buffer zones for temporary storage can accommodate unforeseen delays, maintaining the efficiency of the cross-docking operation.
The success of a cross-docking operation largely depends on how well the facility design addresses these challenges while maintaining efficient product flow and minimizing handling time. By implementing thoughtful design strategies and leveraging appropriate technologies, businesses can optimize their cross-docking operations to achieve greater efficiency and responsiveness in their supply chains.
Did you know?
In cross-docking operations, goods often spend less than 24 hours in the terminal before being dispatched to their next destination. This rapid turnover significantly reduces storage costs and accelerates delivery times, enhancing overall supply chain efficiency.
How can we help improve your supply chain operations?
Schedule a consultation or contact Tompkins Solutions for more information.
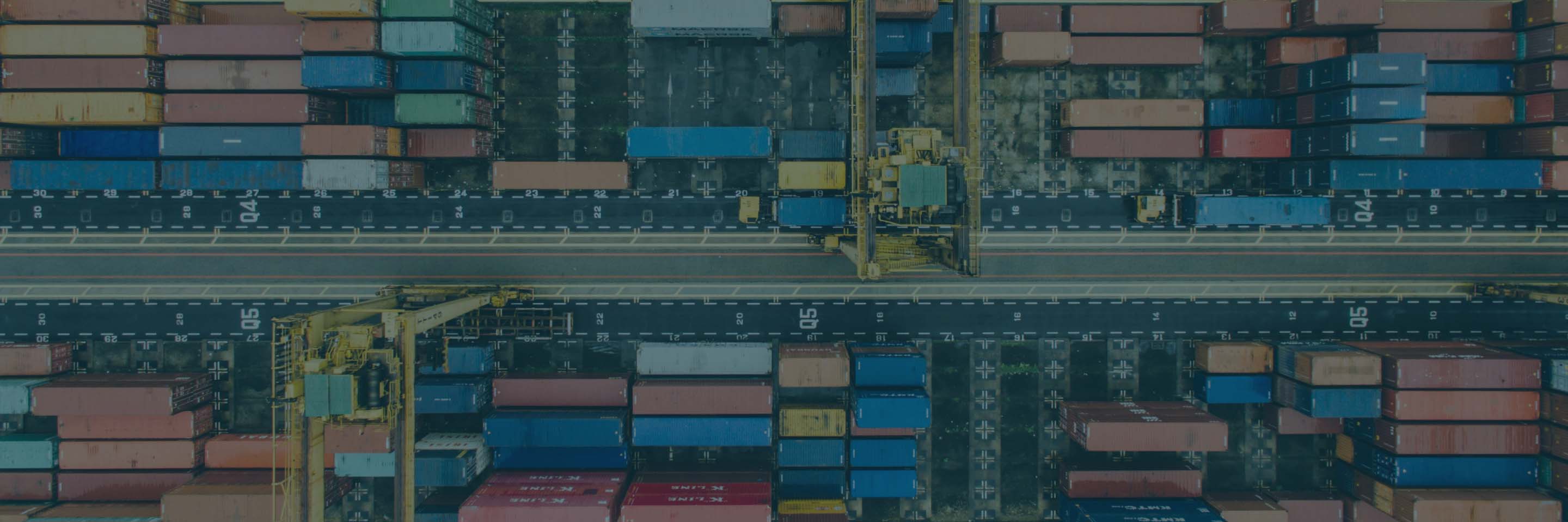
Featured Posts
Discover valuable resources to enhance your knowledge.