Integrated Solutions for Today's Warehouse Automation Challenges
From planning through execution, Tompkins Solutions is here for you and your supply chain challenges.
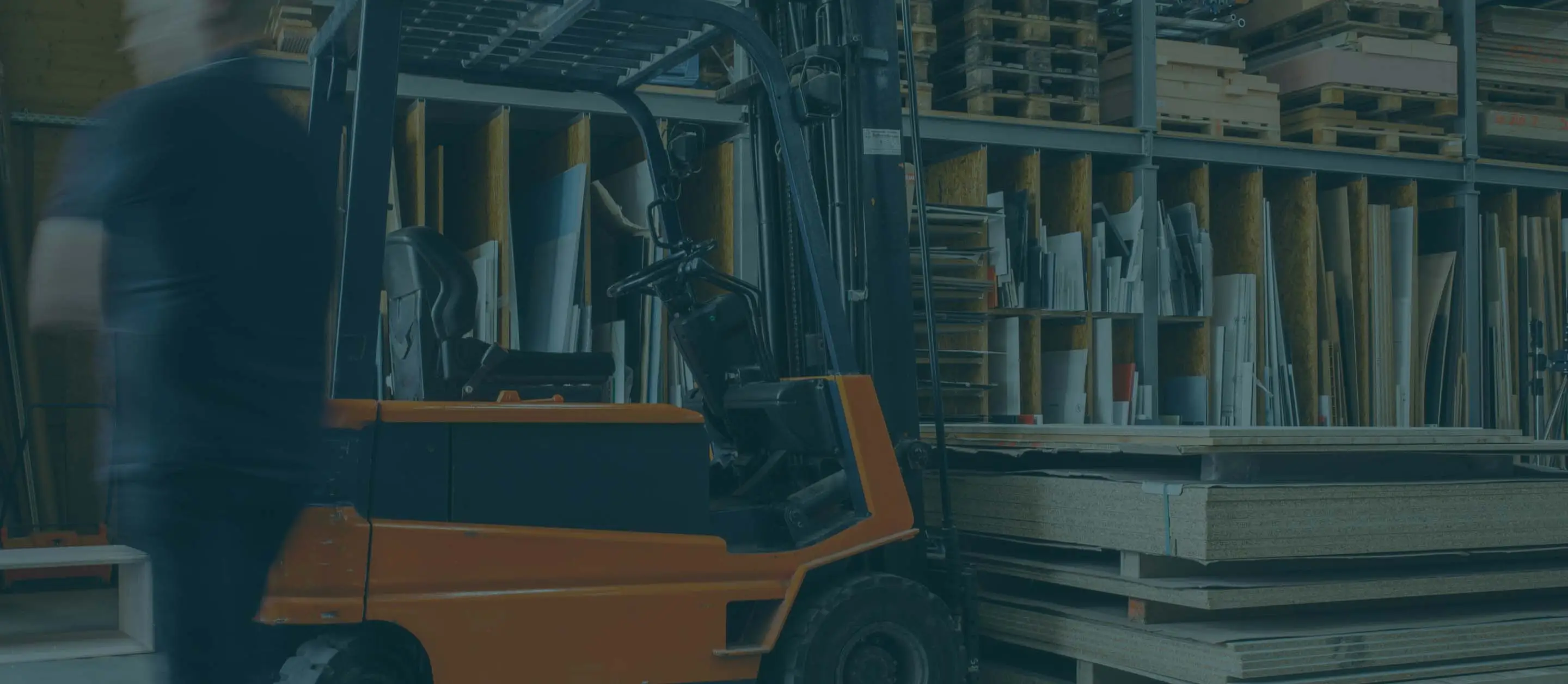
Upgrade Your Storage & Retrieval
Maximizes space and operational efficiency with automated storage and retrieval systems combined with mobile robotics.
Automated Storage and Retrieval Systems (ASRS)
Maximize your efficiency and address challenges like space management, labor shortages, and safety risks with ASRS systems.
Autonomous Mobile Robotics (AMR)
Leverage the next generation of floor robots, sorting robots, automated pallet jacks, and autonomous forklifts to drive more efficient processes.
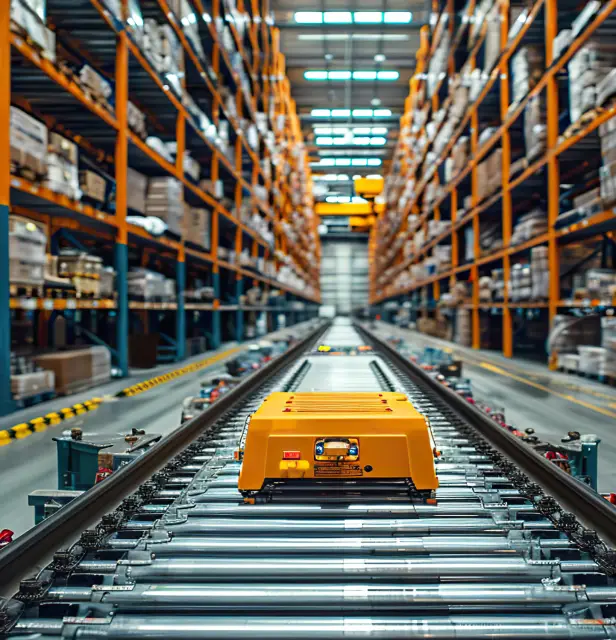
Integrated Pick & Sort Solutions
At Tompkins Solutions, we leverage a range of innovative technologies and hardware solutions to address your unique warehouse automation challenges. Our integrated approach ensures seamless integration and optimal performance.
Sortation
Accelerate sorting processes, ensuring faster and more efficient distribution.
Pick Assist
Increase picking accuracy and speed with modern goods-to-person robotic systems.
Piece Picking
Ensure precise and efficient picking of items, enhancing overall productivity.
Optimize Your Inventory Management
Provide real-time inventory tracking and management, optimizing warehouse operations.
Inventory Solutions
From modern RFID to new drone solutions, new technologies enable real-time inventory tracking for overall warehouse management efficiency.
Palletization
Automate stacking and pallet organization, enhancing warehouse efficiency, space utilization, and handling speed.
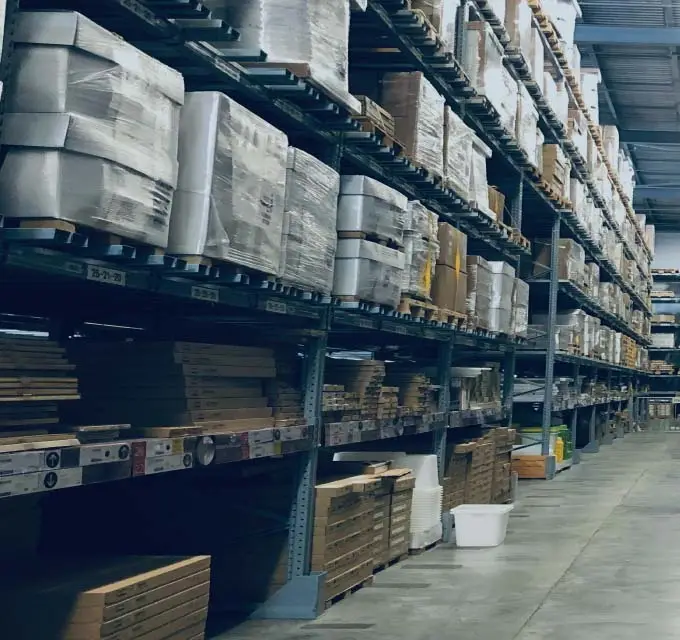
Innovation Lab: For Next Generation Automation Solutions
At Tompkins Solutions, we're helping deliver the latest in automation technologies by exploring next-generation solutions that will solve both problems today and in the future. Our Innovation Lab explores the latest cutting-edge technologies and works with forward-thinking customers to bring the future to today.
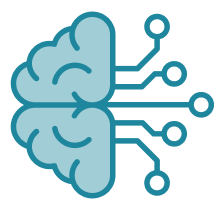
Artificial Intelligence
Explore modern AI tooling systems like OpenAI, Gemini (Google), Llama (Meta), and others to find new solutions to challenging problems.
Internet of Things
More and more sensors have increasing computing power and connectivity, providing an opportunity to gather enormous data that will lead to insights.
Humanoids
Emerging humanoid solutions provide new ways to complement your workforce, enabling your human capital to achieve greater efficiency and productivity.
Our Technology & Innovation Partners
We work with industry leading technology partners to build integrated solutions that solve our customer's unique challenges.
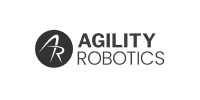
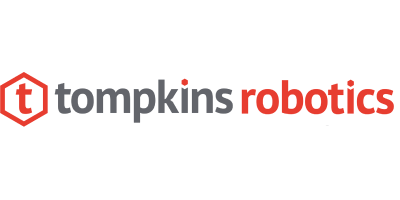
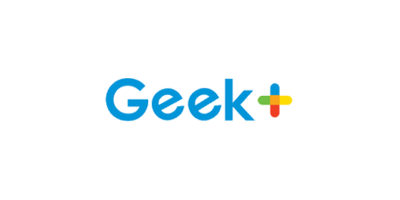
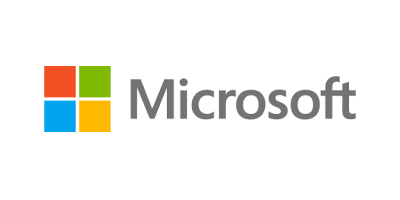
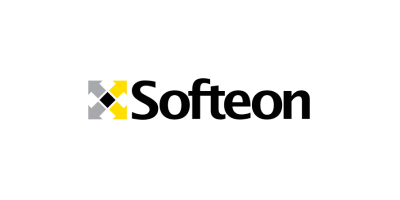
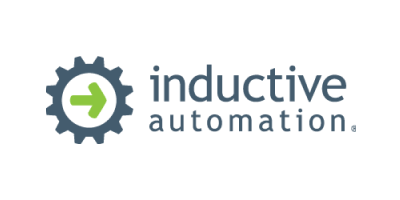
Optimize Your Warehouse Operations
Schedule a consultation or contact Tompkins Solutions for more information.
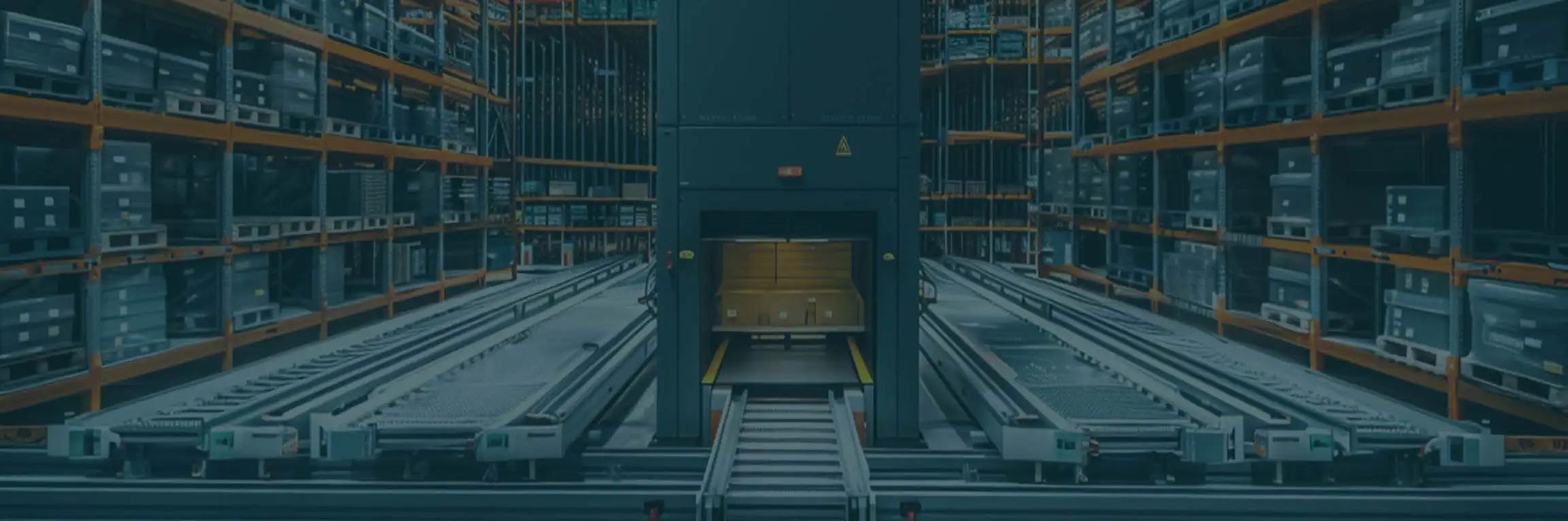
Featured Posts
Discover valuable resources to enhance your knowledge.